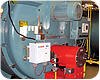
Millipore’s 80 ashby rd. plant in
bedford, ma, post retrofit.
When a burner/boiler retrofit exceeded expectations at a biopharmaceutical facility by reducing emissions and delivering a 31% reduction in fuel costs, the company naturally started taking the approach to other locations.
The Millipore Corporation, headquartered in Billerica, MA, is a life sciences leader in providing technologies, tools, and services for bioscience and biopharmaceutical manufacturing. While Millipore’s main focus is on developing enabling technologies for our most challenging health issues, it is equally determined to be a green neighbor through their sustainability program.
In 2006, Millipore implemented a strategic sustainability effort in order to reduce carbon emissions by 20% by year 2011. Currently, Millipore is poised to smash that goal a lot sooner than expected. The company has performed numerous energy and emissions reduction projects which include compressed air system improvements, lighting controls based on time and occupancy, heat recovery/exchange systems for exhaust air, building envelope improvements, and much more.
In addition to these great conservation measures, Millipore performed a major burner retrofit at their 80 Ashby Rd. plant in Bedford, MA. This plant houses two 300 hp Cleaver Brooks low-pressure steam, natural gas-fired boilers. The first boiler is a standard Cleaver Brooks fire tube manufactured in 1979. The second boiler is a Cleaver Brooks LE (low emissions) model, circa 2001. The LE model has an internal damper above the burner housing that allows flue gas recirculation into the combustion process. This technology is used to deliver lower NOx emissions.
Millipore teamed with George T. Wilkinson, Inc. (incorporated 1951), a nearby service and installation contractor located in Rockland, MA, who has been an industry leader in reducing customers’ fuel costs and carbon footprints. The retrofit involved removing the existing burners and installing new Limpsfield low O2 burners coupled with the Autoflame Combustion Management System and variable speed drives.
Limpsfield guarantees an O2rate of 3% (15% excess air) throughout a boiler’s firing range, designed to deliver maximum heat transfer. Excess air will reduce the residency time of the products of combustion on the boiler tubes, thus sending useful energy out of the stack. Not only will the burner deliver this performance, but it will do so while not producing any carbon monoxide (unburned fuel).
Typical fire tube units can achieve lower oxygen readings at higher firing rates, but at the lower ranges and during modulation, higher oxygen levels are extremely difficult to combat. Limpsfield is not your typical burner, as it offers all stainless steel components and a large viewing port allowing facilities personnel and service technicians the ability to see the burner’s diffuser as well as the flame without removing critical components.
Autoflame provides extremely accurate servo motor technology adhering to proportional/integral/derivative (PID) logic. In addition, Autoflame has adapted its patented Exhaust Gas Analyzers (EGAs), which boast a three-parameter trim (O2, CO, CO2). Variations in calorific fuel values and atmospheric conditions can cause a burner to operate at non-commissioned combustion figures. The Autoflame EGA ensures the burner will operate at service technician commissioned standards at all times.
Finally, the package also included Autoflame’s Data Transfer Interface (DTI), which transports the boiler and burner data from the unit(s) to a personal computer. The personal computer comes fully equipped with Autoflame’s Continuous Emissions Monitoring Software which allows customers to view emissions data by chart or graph. A client can trend their emissions while keeping a watchful eye on fuel flow, steam flow, and numerous other parameters that customers find imperative to boiler/burner operation.
In order to measure the successes of the retrofit, Millipore and National Grid hired a local and independent engineer to perform a study which included historical gas usage, metered electrical data, combustion gas test data, manufacturing history, and degree days. The result after six months: a staggering 31% reduction in fuel costs and a significant reduction in boiler emissions.
Paul Lukitsch, Millipore’s regional facilities manager, has been astounded with the results. “Originally, we planned this project to achieve about 12% to 14% fuel savings. We knew that our boilers were very well maintained, and did not expect to exceed this. Well, when the data was rolled up by the engineering consultant, we have been very impressed with the results. To this, we have installed similar systems on four more large boilers in Massachusetts, and will be looking to standardize this technology at all of our sites worldwide,” he said.TB