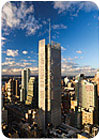
The exterior of the New York Times Building features low-iron, clear glass that has a transparent effect and a ceramic rod screen that acts as a sun shade and reduces the thermal load. (Photo courtesy of © David Sundberg/Esto.)
We often think of news as focusing on what just happened, but the mixed-use building housing the New York Times’ headquarters puts the emphasis squarely on what’s possible right now and where smart design is headed. The ability to go off-grid when it wants and a sophisticated daylighting system coordinated to heighten HVAC performance are just two exceptional components, not to mention Manhattan’s first high-rise UFAD system. The air distribution design for floors serving the newspaper’s offices is even more advanced, so come on in and let the story unfold.
The green building movement is gaining momentum in just about every part of the U.S., from rural communities to big cities. Nowhere is this trend more evident than in New York City, which is home to a large number of environmentally friendly buildings, including the recently completed 52-story New York Times Building.
The building was finished shortly after New York City’s mayor announced his Sustainability Plan - plaNYC 2030 - in December 2006. This sweeping plan is designed to enhance New York’s urban setting by focusing on improving the quality of land, air, water, energy, and transportation. To achieve its goal of reducing greenhouse gas emissions by more than 30% by 2030, the plan will target the city’s largest energy consumers - institutional buildings, commercial and industrial buildings, and multi-family residential buildings - and encourage energy efficiency upgrades through a system of incentives, mandates, and challenges.
By design, the high-performance New York Times Building already incorporates a number of energy-efficient features, including an integrated façade management system of dimmable lights and mechanized shades that responds to the sun’s angle and intensity, an underfloor air distribution system (UFAD), on-site cogeneration, and a highly efficient chiller plant that utilizes both centrifugal and absorption chillers.
Sustainable Design
The New York Timesis one of the best-known daily newspapers in the country. First published in 1851, it is the largest metropolitan newspaper in the U.S. and has won more Pulitzer Prizes than any other newspaper in the country. Given its impressive history, it’s no wonder that when the time came to build a new corporate headquarters in midtown Manhattan, The New York Times Company, the parent company ofThe New York Times, wanted a similarly impressive building constructed.Even though LEED® certification was not pursued for The New York Times Building, The New York Times Co. and its partner, Forest City Ratner Companies, wanted to incorporate numerous sustainable features, as well as provide a comfortable, energy-efficient environment for building occupants. To meet those objectives, world-renowned architect Renzo Piano was hired to design the building, along with architectural firm FXFOWLE, while Flack + Kurtz provided the mechanical, electrical, plumbing, fire protection, and telecommunications design for the green building. Gensler and Flack + Kurtz were then hired directly by The New York Times Company to design the interior fit-out of their half of the overall building, which would be their new corporate headquarters.
In the spring of 2007, New York Times Company personnel moved into their new offices, which are located in 800,000 sq ft on the 2nd through 28th floors. Forest City Ratner owns the remaining 600,000 sq ft on floors 29 through 50, as well as 21,000 sq ft of street-level retail space. Most of that space is already rented out to various tenants. The building officially opened in November 2007.
Two separate engineering teams from Flack + Kurtz were used to design the MEP systems in the building. The core-and-shell team consisted of John Bredehorst, project executive/lead electrical engineer, Gary Pomerantz, co-project executive/lead mechanical engineer, Frank Muscarella, project manager/mechanical engineer, and Vincent Tan, plumbing-fire protection engineer. The interior fitout design team for The New York Times Company-owned space consisted of David Cooper, project executive, Fred Holdorf, project manager/electrical engineer, Eric Mitchell, mechanical engineer, and Gary Rabinovich, plumbing/fire protection engineer.
“The New York Times Company has always been very technologically driven,” said Cooper. “They’ve always been advocates of the latest and greatest technology in their business, and they wanted their building to reflect that. They’ve also always been very responsible in terms of energy consumption, so this became a collaborative effort. The entire team had a similar mindset of making this a sustainable development.”
One of the most prominent features of the building involves its exterior, which is made almost entirely of low iron clear glass. The media strive for transparency of process, so Renzo Piano wanted to capture that essence by designing a building that was as transparent as possible. That transparency is achieved through a curtain wall that is designed with floor-to-ceiling glass on all façades and an exterior ceramic rod screen cantilevered off the glass façade, which acts as a sun shade.
“The ceramic rods are arranged on the exterior side of the glass to keep a significant amount of the sun’s energy from coming directly through the glass and into the space,” said Pomerantz. “They have aesthetic value as well, but their functional purpose is that of a sunscreen. We spent a tremendous amount of time working with the architects on the arrangement of the ceramic rods to optimize their thermal effectiveness with their aesthetics.”
The New York Times Company’s space also makes extensive use of daylighting, and the perimeter is dynamically managed to admit maximum natural light without causing thermal discomfort or glare. This is accomplished through state-of-the-art automated shade and lighting control systems and 100% dimmable lighting.
The shade system and the dimmable lighting controls are fully integrated, so that the shades can be positioned in order to get the maximum daylight in the building with minimum solar contribution to the cooling load, as well as minimum glare on the users’ computers. These systems were developed through complex computer modeling as well as an extensively instrumented mock-up of a full quarter of a floor using the actual curtain wall,” said Mitchell.
Energy-Efficient Systems
Another sustainable feature of The New York Times Building is its 1.4MW cogeneration facility, which is powered by two natural gas-fired reciprocating engines operating in parallel. Heat recovered from the engines provides hot water for the 250-ton absorption chiller in the summer and perimeter heating in the winter.Generating electricity on-site reduces the burden of the utility company to deliver power in the summer months when everyone is using air conditioning. In addition, the recovered heat is utilized to provide a cooling source that reduces the load on the electric chiller plant, and the engines run cleaner than the utility generation system.
The overall plant efficiency is on the order of 85%, and overall generated emissions are reduced relative to comparable utility services for the same load requirements. “Because of difficulties with the local utility provider, Consolidated Edison, the cogeneration plant is not connected to the grid,” said Bredehorst. “It’s a standalone system with separate distribution in the building. It has the capability to be backed up by on-site diesel generators and the utility itself.”

A BAS monitors, controls, and optimizes all of the HVAC systems in the
building, including VAV boxes and alarm monitoring and annunciation.
(Photo courtesy of Nic Lehoux.)
Heat for the building is provided via high-pressure steam purchased from Consolidated Edison. After extensive analysis and negotiation, this proved to be the most cost-effective solution as compared to generating heat on-site.
Low-pressure steam is distributed to the steam coils of each AHU in the cellar and podium roof and is also used to produce hot water for the perimeter heating system. The perimeter heating system consists of fan-powered boxes with heating coils at each floor. The low-pressure steam is also used to serve the humidifiers on the floors occupied by The New York Times Company.
Air Movement And Distribution
Also special to the floors occupied by The New York Times Company is a UFAD system - a first for a high-rise office building in New York City. “In deciding to adopt this technology, as opposed to the traditional overhead system utilized throughout every other high-rise building in New York City, The New York Times Company did its homework,” said Cooper. “Their design team went on a trip across the country and around the world to look at underfloor air installations in commercial office buildings and other types of facilities in order to learn more about their design and construction.”While Flack + Kurtz and Gensler have designed underfloor air systems for many years, these trips nevertheless resulted in a substantial amount of information that the team was able to use in the design and construction of the building. “We talked to a lot of contractors and owners, and we asked them what worked and what did not work - where did they find problems with constructing and operating underfloor air systems? We talked about sequences of construction, how to best seal the raised floor plenum so we wouldn’t lose air through the walls or core areas of the building, like the elevator shafts. There were really good lessons to learn, because you can design a system one way, but standard building practices, sequences, and tolerances must be taken into account or some of the realities of construction could cause a `proper’ design not to work as well as it should,” said Mitchell.
They also learned a new way to distribute air in large spaces such as conference rooms. Swirl diffusers are typically used in a UFAD system to introduce air into the space from the raised floor plenum. However, in large meeting room spaces with high occupancies and loads, the required number of swirl diffusers becomes aesthetically unappealing.
“We took an approach that we saw in a large NATO auditorium in Europe, and we re-engineered it with Gensler for the special spaces of The New York Times Company so that there are no visible diffusers in the raised floor of their board room and other large multi-purpose and conference rooms,” said Cooper. “The floor tile itself is perforated, and the carpet is designed with a special backing to allow the supply air to percolate right up through the carpeting into the space. When you’re in the space, you have no idea where the air is coming from, but it feels great.”
While the UFAD system made economic sense for the spaces owned and occupied by The New York Times Company, there was no tenant demand for this advanced system for the rest of the building. Therefore, the rental office floors are provided with chilled water air-handling systems and traditional overhead duct distribution.
Outdoor air for ventilation of New York Times Company floors is provided by central VAV heating and cooling AHUs, which consist of a pre-filter, medium efficiency filter (85%), heating coil sized for morning warm-up, humidifier, cooling coil, and fan section to supply air to each typical floor fan room. The outdoor air is fully dehumidified centrally so that the floor-by-floor chilled water units can typically run with dry coils, minimizing maintenance and maximizing IAQ. Sensors monitoring CO2 levels (occupancy) and VOCs (air quality) in the return air also positively control the amount of outside air that is delivered to each floor. “This demand controlled ventilation strategy minimizes the energy expended conditioning outside air while maintaining ideal indoor air quality,” said Cooper.
Perimeter areas are zoned with VAV fan-powered boxes mounted in the raised floor plenum for New York Times Company floors and overhead for Forest City Ratner rental floors. For the New York Times Company floors, interior spaces use swirl diffusers for air distribution, and perimeter spaces are provided with floor mounted linear bar grilles located near the window line. For the rental office floors, standard overhead diffusers will be employed with linear diffusers along the perimeter ceiling.

An underfloor air distribution system was used in the New York Times building. To avoid using swirl diffusers in large meeting room spaces, the floor tile instead was perforated and the carpet designed with a special backing to allow the supply air in. (Photo courtesy of Nic Lehoux.)
Maintaining Control
A Siemens APOGEE™ BAS monitors, controls, and optimizes the operation of the HVAC systems and life safety functions in the building. The BAS includes a central control station with standalone distributed processing panels at various locations throughout the building and is capable of monitoring the following:- Automatic logging status of all input/output points;
- Condenser water and chilled water supply and return temperatures;
- Outside air drybulb and wetbulb temperatures;
- Operating air and selected space temperatures;
- All VAV boxes (airflow and temperature).
- Programmed optimized start/stop of all HVAC systems and equipment;
- Lead/lag control of pumps;
- Control point adjustment of supply air temperature;
- Alarm monitoring and annunciation;
- VAV box airflow and temperature adjustment.
Alarms are displayed on the system terminal and printer and are included for key elements in the HVAC system, including reporting of normal status and/or temperature. The system also monitors critical alarms of the building emergency generator and fuel oil system.
Optimization and energy management software allows for optimal start/stop, demand control, and other functions, and the system is programmed for PM scheduling of the building’s HVAC equipment.
The lighting, security, and motorized shade systems are separate from the BAS, and each system serves only its individual function. The lighting control system by Lutron provides dimmable light fixtures throughout, allowing multiple light levels depending on daylight entering the building in the open office space. Individual offices and conference rooms are also provided with local switches, allowing each department to set its light level according to preference. In addition, all spaces contain occupancy sensors to control fixtures when the areas or rooms are not in use.
The motorized shade system by Mechoshade is totally automatic based upon the direction of the sun, solar heat gain within the space, as well as sun glare on the work surface. Sensors have been placed within the interior of the building as well as on the roof of the building to control the system. Occupants within the office can manually control the shades within their zone via local touchscreens in the open office area or local switch within the individual office.
From the design stage to finished building, it took almost seven years for The New York Times Building to be completed, but the entire process was a joy for the design teams at Flack + Kurtz. “It was a pleasure working for such enlightened clients,” said Cooper. “In planning the owner-occupied portion of the building, The New York Times Company was diligent in vetting and embracing new technologies and approaches, so it was a great experience.”ES