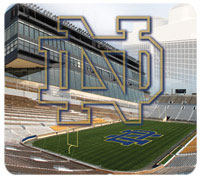
Over the years, reporters covering football in South Bend became accustomed to two constants: strong teams and stifling heat. The journalists’ area offered no viable A/C installation, sandwiched between VIPs above and fans and field below. Finally, the university embraced a VRF cooling strategy in a few places, rescuing students and staff elsewhere on campus as well as our colleagues in the once-oppressive press box.
The University of Notre Dame (UND) has a rich and varied history. Founded in 1842 by Rev. Edward F. Sorin, C.S.C., of the Congregation of Holy Cross, UND is an independent, national Catholic university located in Notre Dame, IN, adjacent to the city of South Bend and approximately 90 miles east of Chicago.
The university is organized into four colleges, Arts and Letters, Science, Engineering, and and the Mendoza College of Business. Also included on campus is the School of Architecure, the Law School, the Graduate School (established in 1918), six major research institutes, more than 40 centers and special programs, and the university library system. Not only are its academic programs first-rate, the university’s athletic program is also widely admired, especially its football program. Notre Dame football teams have won eight wire (AP or Coaches) national championships to go along with more than 800 wins.
Today, the campus comprises 1,250 acres containing two lakes and 137 buildings with a total property replacement value of $2.2 billion.
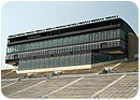
FIGURE 1. The thick concrete floor might have precluded other typical alternatives. The VRF installation avoided the need to cut through it.
FORWARD THINKING
The pursuit of winning outcomes resonates throughout campus and forward-thinking is part of Notre Dame’s history and has been from the beginning. The facilities department is part of this philosophy, according to Anthony Polotto, senior project manager, Office of the University Architect, and all renovation and new construction is planned with an eye toward innovation and energy savings.“The UND campus is crisscrossed by seven miles of tunnels that provide distribution for steam, condensate, compressed air, hot water, and life-safety systems such as fire alarms,” Polotto said. This underground utilities system dates back to the late 19th century, and prior to 1899, each building had its own heating plant. Father Andrew Morrissey, CSC, Notre Dame president at the time, and Father John Zahm, CSC, Notre Dame vice president, felt that this was too wasteful and moved to correct the situation by building a central plant to heat all of the buildings, which was a great achievement at the time, Polotto said. Subsequently, a model of the buildings was sent to the Paris exposition of 1900.
In the 1950s, the university was one of the first in the country to generate its own electricity, which resulted in considerable savings, said Polotto. First, electricity was generated from steam and then later from chilled water.
Today, the university is pursuing LEED® Standard certification in all new construction, according to Polotto. “Because we produce our own power, it is difficult to get to a Silver level,” he said, “However, as we move forward, every building will be LEED certified.”
Conversely, during renovation projects, provisions need to be made to maintain the integrity of the historic structures on campus with an eye toward solving, what Polotto called, “challenge projects” in an energy-saving way. One such project was the renovation of the Notre Dame football stadium press box.
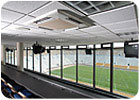
FIGURE 2. A constant air wash keeps the temperature constant in the glass-walled press box.
‘SOLAR OVEN' SINGES PRESS
UND’s power plant chillers supply chilled water at 42°F to 60% of the campus square footage, which leaves a considerable portion not air conditioned. Many of the buildings on campus were designed before the arrival of A/C, said Polotto, with the press box being one such space.The stadium was built in 1930 to replace Cartier Field, where Knute Rockne coached, as it was deemed too small, only holding 30,000 fans. Architecturally, the stadium was built to mimic the University of Michigan stadium on a smaller scale, at first holding 54,000 fans, although an additional 21,150 seats were added in 1997.
The three-level press box is a large steel and glass structure overlooking the field. The top floor is the VIP donors’ level. The middle level broadcast floor includes the emergency medical services (EMS) center, broadcast center, visiting athletic director’s suite, visiting coach’s box, and the Notre Dame head coach’s family suite. The bottom floor houses the stadium’s press box and can accommodate as many as 330 reporters and staff. Temperatures in the press box often soared to over 90° during games, and the large glass wall did not open to allow fresh air into the space, and although large fans provided some relief, the poor IAQ was not alleviated.
The construction of the press box presented challenges which influenced the type of A/C system that could be installed in the space, according to Paul Quigley, regional sales director with Goodman Manufacturing Co. L.P. Quigley was with Excelsior Manufacturing & Supply Corp. of Elkhart, IN, one of the specifiers for the press box project.
“The first problem we faced was the fact that the Notre Dame Football stadium’s press area is three floors below the roof level,” said Quigley. Installation options were limited because the area surrounding the press box is composed of fan seats, perimeter sidewalks, and the field itself, so engineers looked to the roof of the stadium. However, the thickness of the concrete of each floor precluded the option of placing the cooling system on the roof because of the amount of labor needed to cut through three levels of concrete to install ductwork for the system. “Duct systems capable of handling over 80 tons of cooling would be considerably large, take up a great amount of critical finished space, and would also be very unsightly,” Quigley added.
A second problem facing the design team was the significant load diversification due to the layout of the room. The press area has one complete wall of glass, floor to ceiling, facing the fields. “It is a virtual human solar aquarium,” Quigley said. Traditional ducted systems cover areas in a broad-spectrum pattern, which meant that the constantly shifting solar and human load would cause multiple comfort problems due to the fact that air source units don’t do a very good job handling load diversification, he added.
In addition, Notre Dame alumni offered to donate all of the air source rooftop units necessary to get this project completed, so the design team was able to focus on finding the right design for the project, Quigley said. Two recent installations at the stadium pointed toward an answer.
LOCAL CONTRACTORS TO THE RESCUE
The way the university’s prior “challenge projects” were handled ultimately solved the press box problem, Polotto said, thanks to the university’s local contractors who brought new technology to the university’s attention.One such project was the renovation of the medical treatment rooms on the second level of the press box in 2003. EMS personnel are on-call 24/7 and monitor over 750 events on campus each year. Of the three treatment rooms, only one was air conditioned, leaving the other two to suffer high temperatures and poor IAQ. Additionally, the broadcast booth command post where EMS personnel monitor games was uncomfortable due to the lack of A/C and carried with it the requirement that it must be as soundproof as possible for personnel to hear transmissions.
Because of the stadium’s construction limitations, split-ductless systems were specified for the space. Ideal Consolidated, Inc. acted as lead HVAC contractor for the installation, installing three Mitsubishi Mr. Slim systems. According to the Tom Gottfried, regional manager for Mitsubishi Electric HVAC, who specified the equipment with Quigley, the units are suited for historic structures and require no ductwork.
A similar situation presented itself during renovations of Cushing Hall, home to the School of Engineering. Heavy-duty cooling was needed because of the building’s large computer lab and several research labs filled with computers. “We first had to convince the Notre Dame engineering professors that a heat pump was the best solution to their problems before they would consider installing the system,” Quigley said, prior to specifying Mitsubishi’s CITY MULTI VRFZ R2 Series variable refrigerant flow (VRF) system for the installation.
VRF systems are more complex versions of ductless multi-split systems, and are most widely used in air or water cooled heat pumps or condensing units with heat recovery. As the system name suggests, the outdoor unit must have the capability to deliver a variable flow of refrigerant depending on the demand of the indoor units. Multiple indoor units can be connected to a single outdoor unit, making the systems suitable for use with large, multi-zone commercial spaces. (Goetzler, 2007)
When in the cooling mode, refrigerant flows to the indoor units, with the amount controlled by an electronic expansion valve located inside the unit. When the refrigerant enters the coil, it experiences a phase change (evaporation) which extracts heat from the space, thereby cooling the room. The heat extracted from the space is exhausted to ambient air.
When in the heating mode, indoor units are supplied with hot gas refrigerant, controlled by the same electronic expansion valve, which turns to condensation and releases heat energy into the space.
VRF heat pump systems permit heating in all of the indoor units, or cooling in all of the units, but not simultaneous heating and cooling, while VRF heat recovery systems provide simultaneous heating and cooling as well as heat recovery to reduce energy use during the heating season. (Amarnath, 2008)
VRF systems, popular in Asia and Europe for years now, are gaining a following in the U.S., and after the successful installations on the UND campus, thanks to UND’s local contractors, the school decided to install a CITY MULTI Y-Series system in the third-level press box. Ideal Consolidated Inc. took delivery of the equipment in late 2006. Martell Electric handled the electrical systems, Specialty Systems of South Bend was in charge of the insulation, and Ziolkowski Construction provided general trade support for the press box project.
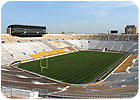
FIGURE 3. Notre Dame alumni donated equipment to solve the IAQ and temperature problems in the football stadium press box.
GAME TIME TEST
The installation was completed in 2007, just in time for the annual spring football game with 200 members of the press in attendance.“When we started up the system around 8 a.m. on game day it was 83° in the press box. By 10 a.m. it was 67°. At game time it was 67° with a packed room. At the end of each quarter it was still 67°. All systems performed flawlessly,” said Bruce Heberle with Excelsior.
For his part, Quigley is happy with the VRF system, which solved both of his installation problems.
“The system allowed us to move refrigerant instead of air, which meant we could make the same precarious journey from roof to press room with eight small 1 7/8-in. copper lines instead of multiple 4-ft by 3-ft supply and return duct runs, solving the installation problem,” Quigley said.
Inside the box, specific air handlers were placed in front of the glass to give the glass area a constant air wash, while air handlers installed in other areas of the room did not need to be load intensive. All of the air handlers incorporate linear expansion valves, which means they produce the precise amount of cooling that each area needs at all times.
“This is a huge energy saver, since the glass load goes from extremely intense to rather mild depending upon the time of the day, and the location of the sun, and the units only work as much as is necessary to produce the amount of cooling needed to handle the load,” Quigley said._
At times when the load is low, the inverter compressor, and air handlers cycle down as low as 16% of their rated capacity, meaning 84% less energy used. “This solved the comfort problem,” he added.
As for the offer of donated equipment, which doesn’t happen every day, Quigley said that free equipment is pretty tough competition for a bid. However, due to the creative, practical, and functional solutions made possible by the VRF system, Notre Dame turned down the offer for the free air source rooftop units and opted to invest in this technology instead. “They knew they were money ahead for years to come, and the integrity of the building would not be affected by our installation,” he added.ES
SIDEBAR: News From The Underground
There are more than seven miles of tunnels underneath the Notre Dame campus housing various distribution systems. The main tunnel system includes steam, condensate, compressed air, domestic hot water, fire alarm system, and telecom and IT systems. The various distribution systems include:- Ricwel system, which is a direct buried steam and condensate piping system -8,000 ft;
- Chilled water distribution - 62,000 ft;
- Domestic water distribution_- 130,000 ft;
- Electrical distribution - 148,000 ft;
- Storm sewers - 121,000 ft;
- Sanitary sewers - 87,000 ft.
BIBLIOGRAPHY
Amarnath, Ammi, and Morton Blatt, “Variable Refrigerant flow: Where, Why, and How,” Engineered Systems, February 2008, Vol. 25, No.2:54.Goetzler, William, “Variable Refrigerant Flow Systems,” AHSRAE Journal, April 2007:24.