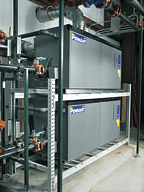
Today, the hydronics industry has emerged from its extreme makeover, moving at warp speed with confidence and clear direction. It's now characterized by the emergence of new equipment and market conditions that have driven manufacturers to new levels of engineering excellence.
Without question, market forces - chiefly, the push for higher and higher energy efficiencies, and demand for equipment to go where no equipment has easily gone before - are driving the pace for new and innovative hydronic solutions.
The newest generation of hydronic equipment (such as condensing technology that purposefully extracts heat from condensate within the system) has pushed combustion efficiency into the 95% to 99% range. That's smart use of energy. Add new controls to the picture and integration with BAS, and you begin to see how quickly this market is moving.
With efficiency performance like that, building owners are now at attention. When the design engineer can calculate a three- to four-year payback for new equipment (or perhaps even shorter than that in some instances), there's real incentive to install new technology.
The commercial construction market has been relatively strong. As part of that, we're now seeing much higher interest in large radiant heat and snowmelt systems, forces that push forcefully at what, just a decade or so ago, seemed to be a dying, replacement-only industry.
But before our excitement about new technology moves ahead of itself, let's take a step back and ask, "What is the concept of high performance in terms of hydronic heating?"
To answer that question, among many others, we'll tap the experience of several industry experts. They are:
- Bill Root, vice president of sales and marketing, Laars Heating Systems Company;
- Mike Chiles, president and general manager, Watts Radiant;
- Len Petersen, national sales manager, Grundfos Pumps Corporation;
- Tim Rosen, P.E., Concept Mechanical;
- Rex Gillespie, director of marketing, Caleffi Hydronic Solutions; and
- Joan Mishou, manager of applications engineering, Laars Heating Systems Company.
You'll learn that high performance hydronic heating and volume water heating depends on the interrelationship of six key facets of the boiler system.
System Efficiency
How effectively the boiler relates to the total system is determined by its capacity to deliver heat either quickly, or slowly, depending chiefly on the needs of the system and the ability of the boiler to adjust to changes in the system's demand for heat. The common term is "to size to the load." Also, total system performance is enhanced when the equipment works at peak performance - with fuel consumption happening at the highest levels of combustion efficiency - at all levels of heat demand.According to Mishou, another important factor is more sophisticated controls that sample changes over time and "learn" the responses of the system to changes in conditions such as heating load, outdoor air temperatures, and firing stages of the boiler(s).
"And, of course, there's modulation or staged firing vs. on-off," said Mishou. "This is perfectly illustrative of the giant strides the industry has made during the past couple of years. Modulating and staged-fired boilers reduce fuel consumption by ‘sizing to the load' so that the amount of heat produced by the system precisely matches the need."
Piping and pumping are also key factors in building an efficient system. The most efficient boiler in the world can't make an entire system efficient if the system is not piped and pumped correctly.
And, there's response to outdoor temperatures, water storage temperatures, and system loop temperatures. These, too, are very important contributors to overall system performance. Control systems should be sufficiently advanced to account for, and take into consideration, these key variables.
"Condensing boiler technology is one of the key factors for the dramatic increase we see in boiler/water heater system efficiency," added Root. "Condensing boilers, like our new Rheos+, are built to encourage the formation of condensate within the system and to withstand the corrosive nature of the liquids that form there. "Latent heat is extracted from the moisture that forms in either the primary or secondary heat exchanger, dramatically enhancing combustion efficiency," he said.
But efficiency is only one of the advantages of installing these systems. Application of the boiler can play an even more important role. "Their tough resistance to thermal shock and the ability to accept low return water temperatures puts them in a category of their own and opens up many new possibilities for high-volume, cold-start systems. One example is a commercial snow melt system," said Chiles. "A condensing boiler takes very low inlet temperatures in stride - in fact, the lower temperature of incoming water (or a water/glycol mix as is usually the case), the higher the combustion efficiency of the boiler."
And, according to Mishou, because all condensing boilers use combustion-air fans, many boilers have an exceedingly long vent reach.
Modulation goes hand in hand with the ability to operate in a condensing mode. When boilers can operate with low return water temperatures, and lowered firing rates, the relationship of heat transfer surface to fuel consumed, and the combustion efficiency itself combine to deliver maximum efficiency. And, when multiple boilers are installed, each one handles only a portion of the heating load; that drives system efficiency even higher.
"Some systems that require higher operating temperatures most of the time may still benefit from a ‘lead boiler' that's a condensing boiler," continued Mishou, "while the remaining boilers that provide the bulk of the heat are non-condensing."
Combustion Efficiency And Thermal Efficiency
Just a few years ago, many of us in the industry considered combustion efficiency and thermal efficiency to be the most important factors in determining overall system performance. That's not the case today.According to Root, transferring heat from a boiler into a total system - and in just the right amount and at just the right time - is a truer measure of high performance.
But if you want a high performance system, it only makes sense to start with a high-performance "engine." Manufacturers today put a lot of engineering effort into maximizing heat transfer to water - and that efficiency is a critical aspect of a boiler's performance. The only thing to keep in mind is that many applications do not call for the highest levels of combustion efficiency (condensing equipment) because the water temperatures are too high. Designing systems with staged firing, modulation, and/or multiple boilers can often produce higher system efficiency than trying to use a single condensing boiler that claims higher combustion efficiency.

Green Boilers
"Green" boilers are another facet to the high performance equation. "Today, when this topic is discussed at industry round tables, we look at emissions - NOx, CO, CO2- with the real desire [to] see lower levels of pollutants that endanger our atmosphere and indoor air quality," said Mishou. "California's South Coast Air Quality Management District (SCAQMD), the states of Nevada and Texas, and selected projects in almost every other state, have set limits for emissions, especially NOx. And, being able to take 100% of the air for combustion from outside the building is also required in many installations."Information Exchange
How well does the boiler act as part of a system in terms of both accepting and responding to external sources of information? "Information exchange," if we really put it to the test, refers to the boiler's ability to both receive external information - such as outdoor air temperature, new instructions from a BAS, and system zone information - and to send information back to the BAS - such as inlet and outlet water temperatures, operating cycles, fuel consumed, pump operation, etc.According to Root, these functions play an important role in the exchange of information to and from the system, such as the following:
- Ability to accept communication signals from BAS (BACnet, LON, Metasys, Echelon).
- Ability to report information back to the BAS.
- Collection of data that provide management information about operating statistics and efficiency, such as inlet and outlet temperatures, run time, percent load, domestic tank temperatures, system loop temperatures, etc.
- User interfaces - How well, and how easily the user can change operational settings, is important. After all, we need to see and discern what the boiler is doing. As part of this, ask: How easy is it to learn the boiler's command system? Is it intuitive and customer-friendly? Consider the function and usability of the keypads, displays, and convenience of access. Will the installer, service contractor, or plant maintenance supervisor, for instance, find themselves standing in front of boiler at eye level, or on their knees with a flashlight, to see what the temperature is inside the unit?
Installation and Serviceability
Ask a field technician or building maintenance supervisor to tell you his impression of what constitutes "high performance." No doubt, the conversation will quickly swing to those parts of the system that they consider an enhancement to overall function and design, or a frustrating lack of consideration for their need to get in and out of the boiler (perhaps with a few expletives thrown in for good measure).These factors contribute to ease of boiler installation and service:
Cabinet access. Can you easily reach and replace key components? Seeing all of the boiler's components is very important, but physically getting them out of, and back into the boiler without standing on your head or skinning your knuckles is often an entirely different proposition. Service-friendly boilers make happy customers!
Field wiring connections. Wiring-in thermostats, field interlocks, accessory equipment, and BAS control wires should be easy and require little additional time.
Optional water piping, gas, and electrical connections. Can you connect water, gas, and electric to different sides of the boiler, if necessary? No doubt, some sites aren't very accommodating. Gas, water, or electric connections always seem to be on the wrong side. Admit it: The boiler that gives high performance can accept alternate side piping and gas connections easily.
Filters. Combustion air should be filtered to prevent debris from getting trapped in fans and burners, and the filter should be washable and reusable.
Installation: indoors or outdoors? Many systems require that boilers be placed on a roof or outdoors on an equipment pad to preserve costly interior floor space. And, in many retrofit and fuel conversion projects, adequate boiler room space simply isn't provided. This may force the remote location of key heating system components, pushing them outside the building envelope. Of course, venting options are part of the location decision: a high performance boiler should allow for sidewall and vertical venting, as well as installation outdoors.
Simply put, a truly high performance boiler needs to be installation- and service-friendly. And, it needs to be an efficient part of the overall system. Remember, long after the initial installation costs are paid and forgotten, service costs will continue for the life of the boiler. These should be evaluated at the time of initial purchase.
Venting. What are the options? Are you given the choice of sidewall, vertical, indoor/outdoor? You should expect it.
The Boiler, In Context
Of course, what exists beyond the boiler jacket and near boiler piping will impact overall system performance. Consider circulation, control solutions, and heat distribution. New technology and intelligent system design are the key players here.
Multispeed Circulation
One of the most important facets to optimal circulation for hydronic systems is for design engineers and installing contractors to match a pump's performance, or flow characteristics, to the specific job that it needs to perform within the system.According to Petersen, a single-speed pump has one performance curve - a measurement of head (ft) and flow (gpm) - and operates at that level only for a particular condition. But, he said, new multispeed circulators, such as Grundfos' SuperBrute and the larger VersaFlo, offer a much broader range of performance. With the flick of a switch, various speeds can be chosen, easily changing head and flow to meet the specific needs of the system.
"We've standardized on multispeed circulators because we feel they do the best job," said Tim Rosen, P.E., a partner in the plumbing and mechanical contracting firm, Concept Mechanical, based in Avon, CO.
"Three-speed circulators give us greater control and versatility," added Rosen. Rosen said that he always does the math, calculating heat loss, flow rate, and pressure drop for each pump.
"I use this information and the stated pump curve to select the proper pump for each load," he continued. "In the past, we might have three or four different pump models on one job, all selected to match the exact needs that we've determined. With multispeed pumps, I can use one pump and select the speed to match the flow and head that we want. And, the use of multispeed pumps allows for future expansions, changes, and retrofits in stride."
Enhanced Piping Solutions
One of the new high-performance devices in the mechanical room combines a hydronic separator and distribution manifold. Called the HydroLink, from Caleffi, the unit is attached to hydronic heating or A/C systems to permit different heat adjustments for separate, multiple zones when there is only one boiler or chiller.Its configurations are compact and can easily be designed into any type of hydronic circuit. The key operating principle, said Gillespie, is that when a single system contains a primary generating circuit with its own circulator and a secondary circuit with one or more distribution pumps, conditions may permit interaction between the circulators, creating unwanted flow rate and pressure abnormalities.
The HydroLink provides a low-pressure loss zone, enabling both primary and secondary circuits to be hydraulically independent of one another. Yet the unit combines both a low loss header and a distribution manifold. A low-loss header is critical for high flow-resistant, low-mass boiler installations because it moves the point of lowest pressure drop from the boiler to the HydroLink's low pressure chamber. The distribution manifold has closely spaced tees, which connect the secondary circuit to the primary loop internally so that flow in the primary loop has very little tendency to induce flow in the secondary circuit.
"Because the unit's openings are so close together, there is almost no pressure difference between them, thus the pressure differential across the internal headers is close to zero," said Gillespie. "The pressure increase created by a given zone circulator is almost entirely depleted by the time the flow returns back to the distribution manifold. This arrangement prevents interference between the boiler circulator and whatever zone circulators are operating."
Heat Distribution
The hydronic industry's renaissance is, in part, due to the reemergence of the radiant heat industry. In the commercial sector, large radiant heat systems place unique demands on a boiler or series of boilers. According to Chiles, these systems were historically characterized by cold starts with long boiler run times, high water volume, high mass, cooler required supply water temperatures, and short boiler cycle-times when the mass is at temperature. Come to think of it, all the ingredients for a boiler's worst nightmare.Of course, large radiant systems require a boiler or boilers with high output. A key advantage, however, is that when the thermal mass of a floor or heated surface has reached temperature, shorter and less frequent boiler cycle times are required. Better yet, a boiler system with modulation permits the heating, and later heat-maintenance of the heated surface. Either a fully modulating burner, or the lead-lag staging of boilers, would allow a system to meet ever-changing load requirements for optimal system efficiency. Another option is to add mass to the piping system to increase boiler run times during periods of low demand. For this, water tanks can easily add mass to a piping system.
"Snowmelting systems pose a different challenge: high demand and high mass with extremely cold water/glycol temperatures," added Chiles. "Here, the challenge is not short-cycling of the boiler. Thermal shock happens when freezing return-water temperatures come crashing into the heat exchanger in a long, hard, cold start."
Fortunately, the new generation of condensing boilers takes this brutal jab in stride. Many modern boilers are not susceptible to thermal shock, due to the materials of their waterways and heat exchangers. Others can be easily protected from thermal shock with the use of a boiler bypass, which mixes hot fluid with the cold system return, allowing the user to meet the manufacturer's minimum return temperature requirements. The bypass can be built to operate automatically, with the addition of a control system, or can be a manual, fixed-temperature system.
Plan Area Requirements (Required Floor Space)
A boiler on a roof, or outside on a pad somewhere is often out-of-sight and much less a frustration for those whose focus it is to preserve interior space for income-generating purposes. This battle has become more antagonistic over the years. Gone are the days when mechanical room space was provided generously! The use of floor space is guarded fiercely, both in new construction and retrofit applications. Mechanical equipment must stand up to the scrutiny of space-savers.Ask yourself, "Is the boiler efficient in its use of valuable floor space?" Consider these characteristics:
- Cabinet volume and footprint
- Required clearances to combustibles
- Required clearances for service (top, sides, front, rear)
- Racking or multiple boilers - essentially, this translates into how densely Btu can be packed into a given amount of space.
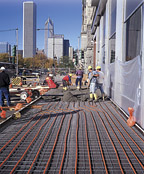
High-Performance Rating Scale
What's in a high-performance system? Here's a quick checklist to summarize system design and function. How well does your boiler system - hydronic or volume water heating - measure up to each of these criteria?- System efficiency (considering also: controls, circulation, and heat distribution)
- Control logic system
- Modulation or stage firing
- Thermal efficiency
- Outdoor air temperature reset
- NOx emissions
- Venting: sealed combustion vs. atmospheric (Cat. I, II, III, IV)
- Accepts commands directly from BAS
- Sends information directly back to BAS
- Footprint size, and - can the heating systems be racked to increase density of Btu/sq ft?
- Filtered combustion air
- Wiring/water and gas connections - what are your options?
- Venting options.
So, where's the hydronic and volume water heating industry headed?
"My crystal ball says that as we move further into the new millennium, boiler designs will deliver higher and higher levels of performance," said Root. "This will be measured by everything we could possibly ask a boiler to do - from basic efficiency to control features, diagnostic and service access, installation flexibility, clean emissions, communication to and from building control systems, and continued enhancements to all of the essential equipment that interacts with the boiler."
Wake up, Maytag Man! We're sending you to class and giving you a new job description. There's work to be done. ES