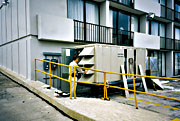
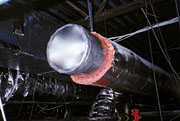
Contributing Factors
It is commonly recognized from current standards and research conducted by the American Society of Heating, Refrigerating and Air-Conditioning Engineers (ASHRAE) that IAQ problems in buildings result from the improper design, construction, and/or operations and maintenance of a facility and its hvac systems.Factors contributing to IAQ problems in buildings that we have investigated or surveyed frequently include:
- Inadequate or improper control of outside air for ventilation.
- Improper control of relative humidity (rh).
- Building pressurization problems.
- Lack of proper automatic temperature control.
These and other IAQ woes can be avoided with reasonable measures to ensure that the automatic controls are designed, constructed, and functioning properly to reduce the risks and likelihood of poor IAQ. Our experience with the investigation and remediation of these common problems in hundreds of hotels, schools, and hospitals throughout the United States has helped us to identify several fundamental principles that can be applied to minimize the risks of developing them.
Foremost in these principles of providing a building with acceptable IAQ is proper automatic control of the hvac systems. Pneumatic/electric controls are encountered commonly in older facilities, but are found less and less in newer or recently renovated facilities. Regardless of the type of automatic control system in the facilities, these principles can be applied.
Automatic hvac control systems are typically designed and constructed with one primary function: to control the heating and cooling systems to maintain comfortable space temperatures for the occupants. In some cases, the temperature controls can be designed and constructed to achieve this primary goal, while creating poor IAQ at the same time. With some planning and foresight, the same control systems can be designed and constructed or modified to incorporate basic control strategies that also provide optimum IAQ.
Proper Ventilation
Automatic control features and strategies for acceptable IAQ include proper control of ventilation. This seems obvious, since no other single issue affects IAQ more than supplying an adequate amount of outside air to a building for ventilation. In hot and humid climates, poor IAQ is many times the result of providing more outside air than is needed to meet building codes and ventilation standards.ASHRAE Standard 62-1999: “Ventilation for Acceptable Indoor Air Quality” is a nationally accepted standard of care for ventilation rates, indicating how much outside air per person is required for each type of occupancy. Unfortunately, very few building owners or engineers can state with confidence how much outside air their building is supplying at any given time. This is especially true for variable-air volume (vav) systems or systems with outside air economizers.
Since most of the following recommendations are fundamental concepts, it is surprising to see that they are not universally applied or understood, as indicated by the number of times they have been found during IAQ investigations. All design engineers and building owners apparently do not practice what has been preached for more than a few years.
Interlock the outside air dampers with the air-handling unit. In hot and humid climates, elevated rh’s can result if the automatic outside air dampers are not properly interlocked. In cold winter climates, the improper control of outside air dampers can lead to coils freezing up and result in water damage, which could eventually lead to microbial growth and IAQ problems. Automatic outside air dampers should be opened to the minimum outside air position whenever the air-handling unit (ahu) is serving an occupied space.
For simple control systems, the automatic outside air dampers can be easily interlocked with the ahu motor starter to close when the ahu is off. In a more complex control system with direct digital control (ddc) having more advanced capabilities, a separate time schedule should be set up and programmed for the outside air dampers to be closed whenever the space is unoccupied.
Use carbon dioxide sensors for demand control ventilation. For spaces with extreme variations in occupancy, such as banquet halls or meeting rooms, carbon dioxide sensors located in each zone adjacent to the room thermostat or in the common return air should be used to automatically control the amount of outside air supplied to provide increased ventilation only when needed for higher occupancies.
The cost of carbon dioxide sensors is now reasonable enough to install them in just about any meeting space. A secondary benefit of the demand control ventilation is the energy cost savings that will result from reduced cooling and heating of outdoor air during reduced occupancy rates.
Use outside airflow stations on large systems to monitor the ventilation rate. For critical areas or large central air-handling systems (50,000 cfm or more), airflow-monitoring stations are available to provide outside airflow measurement and indication at a local panel or remotely at the EMS operators workstation. Not only can the real-time outside airflow rate be measured accurately, but the outside airflow rate can be scheduled and controlled accurately to meet a predetermined ventilation rate for a certain period if the number of occupants for an event are known.
Coordinate the automatic controls with outside air damper balancing. Testing and balancing of the automatic outside air dampers on central station ahu’s should be closely coordinated with the control system installer to ensure that the automatic outside air dampers are set to provide the proper amount of outside air flow for minimum ventilation.
Don’t assume that a ddc system with an adjustable outside air damper has been set properly because the EMS displays a percentage open indication at the central workstation. Many digital control systems indicate the minimum outside air position as a percentage of the stroke of the actuator, or as a percentage of the control output signal to the actuator, but this does not indicate the percentage of minimum outside airflow. ASHRAE Standard 62-1999 requires a certain amount of outdoor air per person, not just a percentage of total airflow to the space.

Proper Control of Relative Humidity
Lack of control of rh is perhaps the most common cause of IAQ problems in hot and humid climates, especially in the hospitality industry. Mold, mildew, and fungal growth will proliferate in a building if the rh in the space is allowed to exceed 60% on a regular basis. Dust mites will also become a problem above this level. Musty odors and visible signs of microbial growth on walls, windows, and diffusers are good indicators of a developing IAQ problem, whether a complaint has been reported or not. Individuals with allergies and sensitivities to mold and mildew will be the first to notice these conditions and report complaints.Corridors and guest rooms in hotels are frequently under negative pressure due to an imbalance between the outside air intake and the exhaust system. Corridors and guest rooms are also frequently conditioned by direct expansion air conditioning systems that cycle on in response to the room temperature. Consequently, the air conditioning system may not be capable of controlling the rh in the space, especially at light loads. Since most air conditioning systems are designed to control room temperature, the rh can swing drastically when negative pressure is present, when a large amount of outside air is being supplied through the unit, or during light load conditions.
Install humidistats or other humidity controls where possible. One of the easiest and most cost-effective methods of bringing humidity under control for constant air volume systems during light load conditions is to install room humidity controls to override the cooling system when the rh exceeds 60%. A simple electric humidistat can normally be installed for under $100 adjacent to the existing room thermostat and wired in parallel with the cooling control. Pneumatic humidistats can be installed to override the cooling signal from a pneumatic thermostat using an inexpensive pneumatic signal selector. The heating will remain under the control of the thermostat to provide reheat if needed during light load conditions.
In more sophisticated control systems, the addition of an rh sensor and a modification of the ddc algorithm to include rh control will allow remote monitoring and control of rh at a higher cost, depending upon the accuracy of the humidity sensor. Remember that this will only control rh if the heating coil is in the reheat position (not in the preheat position) and if the heating system is active.
Furthermore, this should only be implemented after steps have been taken to prevent excessive infiltration resulting from negative building pressure. Otherwise, the result will be increased utility costs and shorter expected life for the air conditioning equipment from excessive runtimes. It should also be pointed out that energy codes in some states, such as Florida, have restricted the use of electric reheat for humidity control below 60% rh.
Use variable-air volume cooling systems where feasible. Vav systems inherently provide improved control of rh over constant volume, variable temperature systems since the leaving air temperature is controlled at a fixed temperature. Although this is a byproduct of the normal operation of the vav system, the rh can be controlled by adjusting the supply air temperature to achieve the desired dewpoint temperature in the space.
The cooling capacity of a vav system is regulated by varying the volume of the cold supply air to each room. Vav terminals for each zone can be provided with or without reheat coils. One project recently completed in a hotel in northern Florida successfully converted an older, constant volume, multizone ahu to vav by providing much improved humidity control in the building.
Proper Control of Building Pressurization
Another common cause of IAQ problems in hot and humid climates is negative building pressure which can result in an imbalance in the amount of outside air delivered through the hvac system and the amount of air exhausted from toilets and other exhaust fans in the building. The building pressurization varies constantly as a result of wind pressures, stack effect, the opening of doors and windows, and the hvac operation.Precondition the outside air supplied to guest rooms and corridors. Outside air systems in hot and humid climates should be provided to serve corridors and guest rooms that provide preconditioned outside air. Sensible heating and cooling can still be provided through the room fancoil or terminal unit. Two renovation projects recently completed in Florida hotels demonstrate how effective this can be in remediation of IAQ problems that have been problematic since the original construction.
In one four-star Florida hotel property located in upscale Coconut Grove, IAQ problems resulted from a combination of excessive infiltration through exterior walls and corridors and guest rooms that were negatively pressurized due to the bathroom exhaust system. The outside air being supplied to the guest rooms and corridors was not preconditioned to remove the moisture before entering the building. A renovation project designed to correct for these problems included installing a rooftop 100% outside air system that provided adequate outside air to positively pressurize the corridors and guest rooms with dry outside air.
An air-to-air heat exchanger in the unit precools the humid outdoor air allowing for increased dehumidification capability of the chilled water cooling coil. The heat exchanger then provides free reheat which results in 40% rh in the corridors and guestrooms. The preconditioning outside air unit also allowed the room cooling systems to be controlled directly in response to room temperature changes without affecting rh (Figure 1).
Another project in a northern Florida hotel involved providing a new rooftop outside air system that preconditioned the outside air for corridors and modifications to the central multizone air-handling system to incorporate vav at each zone to improve humidity control (Figure 2).
Interlock exhaust fans with the outside air dampers. Negative building pressure can occur through the improper design and operation of the exhaust systems in a building. Operating exhaust fans without the outside air being conditioned and supplied through the air-handling system will result in negative pressure in the building. Negative pressure in a building allows uncontrolled infiltration through doors and the exterior envelope of the building. This will typically make the building feel drafty and difficult to heat in cold climates and muggy or musty in hot and humid climates since unconditioned outside air is being constantly introduced into the building through uncontrolled infiltration.
Make sure that all exhaust fans are interlocked properly with the associated ahu’s wherever possible. This will ensure that the exhaust fans operate only when the associated ahu is running or when the outside air dampers are open during occupied periods. This requires the design engineer to zone the ahu’s and exhaust fans to work together, or this may not be possible to achieve when occupancy schedules between zones are significantly different.