Commissioning offers the opportunity to integrate and fine-tune all of the building systems to get the most efficient operation for the entire facility. However, the commissioning process is only as good as the tools that are used in the process. The reliability of the meters, gauges, and sensors used to validate the hvac system directly determines the effectiveness of the commissioning process. With appropriate design, setup, and validation, the bas is a valuable tool in the overall building commissioning process. Significant improvements in building efficiencies can be achieved along with better control of the building environment and fewer complaints from the building occupants.
Specific examples are cited in this article to illustrate elements of the building commissioning process using the bas. Specific projects noted include a cleanroom semiconductor facility and a rare manuscript library housing a priceless collection of rare books. The concepts presented can be applied for commissioning any facility.
Who's Commissioning the bas?
Few argue with the premise that commissioning should be provided for complex building systems. Sophisticated systems that require rigid environmental conditions will operate more efficiently and reliably with proper commissioning. However, in the day-to-day process of building design and construction, there is one item that is often forgotten or simply taken for granted - the "bas as a tool for commissioning" the entire hvac system.
The bas, or direct digital control (ddc), is the building brain. It provides the sensors and controllers that operate an entire facility. It can be integrated with all aspects of a facility to control the building security, lighting, and life safety systems for optimum building performance. The current economic climate of high energy costs mandates that we use the tools available to us to operate our buildings as efficiently as possible. Building commissioning, using the tools afforded by the bas, can routinely return 10% to 30% reduction in utility operating costs over the project that fails proper commissioning standards.
bas in the Building Commissioning Process
Several prerequisite conditions are necessary in the commissioning process. These conditions apply to the validation of the bas when used as a tool in the commissioning process just as they apply to the commissioning process itself. Both the requirements for commissioning as well as the tools to accomplish the commissioning should be established at the beginning of the project. This allows integration of the bas with all aspects of the facility. It also maximizes the potential for efficient building operation and utility cost savings. Essential elements of the commissioning process as they relate to the hvac and bas include the following:
- Identify project requirements.
- Identify criteria that will be used to establish that the requirements are met.
- Design systems that are appropriate for the required environmental control.
- Identify, validate, and commission the system tools.
When each of the elements are established, then the bas can be used to commission the hvac systems in a simple and effective manner. However, even the best of hvac systems will operate inefficiently or simply fail if not properly set up and commissioned. The consequences of this failure can lead to dramatically increased operating costs or the inability to meet basic environmental criteria. In either case, the bas and hvac system cannot be properly commissioned unless the bas tools used to control and monitor the building systems are appropriate, reliable, and properly validated.
The procedures presented here provide a simple and effective process for commissioning the bas. When properly validated, the bas can be used with confidence as a tool for the setup and commissioning of the building hvac system. Table 1 provides an overview of the commissioning process via the bas.

Steps for Effective bas Commissioning
The bas commissioning steps identified in Table 1 require additional discussion. Although the examples used here are based on specific projects, the procedures identified are generally applicable for commissioning any facility.Cleanroom facility: The project is an 8,000-sq-ft research and development facility. It consists of a Class 10 semiconductor cleanroom process plant that includes Class 1 environments at specific equipment. Exotic gasses and other hazardous materials are used, and rigid temperature, humidity, and pressurization controls are required. The main semiconductor process areas are surrounded by Class 100 and Class 1000 utility support areas and related administrative space. The central plant chillers, boilers, emergency power, and maintenance offices are housed in separate structures adjacent to the building.
Rare book library: The project is a 35,000-sq-ft rare book and manuscript library located with a spectacular view of the beach in beautiful Southern California. It requires constant temperature and humidity control to prevent deterioration of the irreplaceable manuscripts. The central plant chillers, boilers, and air-handling equipment are all housed within the main building site.
The commissioning steps noted below will ensure that the bas provides accurate and reliable data. The bas can then be used with confidence as an effective tool for commissioning the hvac and general building systems.
Step 1 - Design qualification (DQ): Evaluates project requirements and establishes the necessary design procedures to meet the requirements.
- Evaluation 1: The project's criteria;
- Evaluation 2: Project user's requirements;
- Evaluation 3: Hvac systems; and
- Evaluation 4: Bas.
The following data taken from the design examples noted above illustrate the elements of the DQ process:
- Project criteria: An evaluation of the project needs identified several critical requirements for the projects. These included the need for a documented method to maintain positive room pressurization in the cleanrooms and room particle count certification. Environmental control criteria for both the library and the cleanroom were established at setpoint + 0.5?F and + 2.5%rh.
- Project user requirements: Specific user requirements were identified and documented. These included requirements for both the technical personnel using the space and the management personnel charged with the overall fiscal responsibility for the facility operation. Among the requirements identified was 24-hr/day monitoring that allows building maintenance supervisory personnel remote, real-time access to the facility controls and monitoring.
- Hvac systems: The hvac system for the example cleanroom project requires definitive control of room airflow and pressurization. Both projects require rigid control of the rate of change of the room temperature and humidity.
- Bas: At this stage, the type of bas is reviewed by all parties concerned. Dedicated ddc systems with fiberoptic LAN connections were selected to interface with the existing facility ddc systems.
Step 2 - Installation qualification (IQ): The IQ of the bas is a documented process to ensure that the components, devices, or programs installed are those designed and specified. The bas IQ process simply requires a diligent point-to-point verification for each element of the ddc system. Each sensor, application controller, and communication signal is tested and documented to ensure that they are correct and function as intended.
In our cleanroom example, a room pressure sensor with a -0.10 to +0.10 psig range and accuracy of +1.0% was specified. The contractor submitted a product that complied with the specified design and obtained approval for installation. If the bas commissioning stops at this juncture, there are many questions that remain unanswered:
Have the installed products been accurately specified? In the room pressurization example, this can include the application-specific controllers, the pressure sensors, the communication network, and the central ddc equipment. Has the correct room pressure sensor been installed? Has it been accidentally switched with a different sensor having different characteristics? Is the sensor wired correctly? Are there any wiring cross connections? What impact will the sensor calibration have on system operation?
Step 3 - Operation qualification (OQ): The OQ process ensures that the bas components and equipment can operate as specified in the design documents. It verifies the calibration and control functions and validates the general operation of the ddc equipment. At this stage each of the controllers must be tested and loop tuned, and the results documented and validated.
This step is frequently ignored, skipped, or simply left up to the discretion of the control contractor's field personnel. The impact in terms of operating costs can be both substantial and transparent. For example, the cleanroom air supply fans may be operating at 6-in. wc of pressure when only 4-in. wc is required. The library hvac may be continuously dehumidifying or reheating the room air supply when no humidity control is required. The impact here is essentially invisible and may continue undetected throughout the life of the project.
The fundamental question is, "How can we validate the operation of the building hvac using a ddc system that is not yet commissioned or calibrated for this purpose?" The answer, of course, is we can't!
Step 4 - Performance qualification (PQ): PQ validates the performance of the entire system after the bas has been properly set up and operating through the DQ, IQ, and OQ processes. This usually involves a 72-hr trending performance test. The system operation is documented to validate that it performs properly as a whole and meets the specified system accuracy and environmental control requirements.
A summary of the four steps of commissioning ddc systems is shown in Table 2.
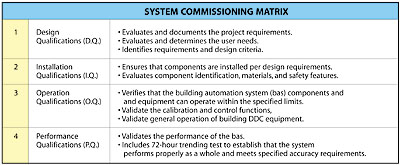
Summary
The procedure for commissioning a facility by means of its ddc bas is simple and direct. If followed properly, the bas can provide an effective and reliable tool to set up complex and demanding hvac systems. Benefits are realized in many different areas, including a reduction in a building's bottom line utility costs and improved proactive maintenance capabilities. Energy savings of up to 30% can be realized for facilities otherwise thought to be properly operating. On the other hand, if the bas itself is not properly validated, the hvac and building commissioning process relies on unreliable data and control, with little hope of meeting complex system requirements or optimizing building performance.ESBibliography
ASHRAE Guideline 1, 1996Hvac Commissioning Process, Atlanta.National Environmental Balancing Bureau (NEBB), Procedural Standards for Building Systems Commissioning, Gaithersburg, Maryland 1993.
Shadpour, Frank, Fundamentals of Hvac Direct Digital Control, Practical Applications and Design, Escondido, CA: Hacienda Blue Publishing, 2000.
Schikora, Jon, "Qualifying High Speed Assembly Machines as Part of Process Validation," Medical Device & Diagnostic Industry, July 2000.
Willis, Lyle and Shadpour, Frank, "Commissioning DDC Systems as a Tool For Commissioning Health Care Facilities,"(unpublished).