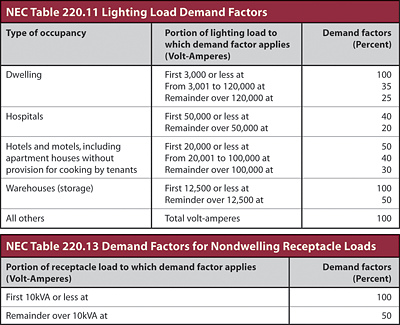
Connected Load vs. Demand
We have all experienced the difference between connected load and demand load across the wide variety of applications in commercial, industrial, and institutional projects. Many factors contribute to this situation, one of them being how the project is designed to meet the owner's project requirements (OPR) vs. how it is operated by the staff after the construction has been completed.Another of these factors is equipment nameplate rating vs. actual load. For numerous applications, there are provisions in the National Electric Code (NEC) to assist in this reconciliation such as the demand factors listed in Tables 220.11 and 220.13 of the current NEC (Figure 1). Whether through the NEC, practical experience, or a combination of the two, many have found the demand to be consistently 25% to 50% of the nameplate value.
Also, with changes in the use of technology and more concentrated occupancy rates, there has been an upward trend in the "watts per square foot" design load. Whereas general purpose power might have been 1 to 3 W/sq ft in the 1970s, it now might be more in the range of 5 to 15 W/sq ft.
Even though ASHRAE Standard 90.1 has effectively contributed to reducing the lighting load, the combined total load for lighting and general power has risen. These trends have caused the industry to adjust their design philosophies in terms of electrical distribution architectures (e.g., localized panels, structured cabling, and modularity) as well as the HVAC support (cooling) for these loads.
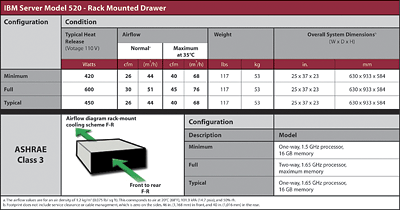
Connected Load vs. Demand for Datacom Applications
In the datacom industry, the combination of these increased load trends and the impact of connected vs. demand load are magnitudes more significant. Datacom facilities were previously designed at 25 or maybe 50 W/sq ft while the spaces themselves were relatively small areas.Today, the datacom rooms within a facility are commonly 5,000 to 50,000 sq ft, or more. Further, the design capacities can be 50 to 100 W/ sq ft, or more. The size of the space, combined with the design capacities, represents a significant challenge, especially when compared to the common design capacities of 5 to 15 W/sq ft for other commercial or institutional projects.
The purpose of this prelude is to establish some general context and not to debate design capacities of various project types. What is important to recognize is that the design loads in datacom applications can be extreme and require careful review, a structured approach, and access to more accurate load information.
As with any project, the process starts with using historical data and experience to establish one or more baseline demand factors. Unfortunately, this is also the start of the problem or challenge. Unlike the old "mainframe days" when equipment was larger and more static, today's datacom environment consists of a greater quantity of equipment, smaller in size, and more flexible in its configuration, the combination of which results in higher concentrations of power.
The previously dominant mainframe environment slowly evolved to a server environment. In the server environment, two or four post racks provide the support housing for multiple servers. These servers can come in different sizes and their height is often measured in vertical space units. The Electronic Industry Alliance (EIA) defines these vertical space units as 1U, 2U, and 4U, etc., with a "U" being 1.75 in. or 44 mm.
This server environment really creates a challenge since a standard rack can support 42U. This means there can be 42 servers that are 1U in size. A source of the challenge is the fact that instead of the rack being fully occupied with 42 servers, it may be partially occupied or could even be empty. This relates to a potential 42:1 variation in load.
Datacom facilities can have dozens, hundreds, or even thousands of servers. This quantity of individual loads, combined with the variation in occupancy and their status (active or inactive), makes it difficult to characterize or trend the load.
Typically, the equipment (and hence the loads) in datacom facilities is actively being changed at a rate far more rapid and significant than traditional commercial and institutional projects. In fact, it is common for datacom equipment to be replaced, or at least significantly reconfigured, every two to four years. This cycle is often referred to as "refresh rate." In addition, various levels of change can easily be taking place every quarter or, in some instances, even monthly.
From this discussion, it is easy to conclude that the load in a datacom facility is a moving target, and any characterization of load in an existing facility in order to establish a baseline is simply a snapshot of an instant in a very fluid environment.
ASHRAE Technical Committee TC 9.9
In 2003, ASHRAE created the Technical Committee TC 9.9 (Mission Critical Facilities, Technology Spaces and Electronic Equipment). Its mission statement is "to be recognized amongst all areas of the datacom industry as the unbiased engineering leader in HVAC and an effective provider of technical information for the datacom industry."The information required for the HVAC design of datacom facilities is fragmented between the datacom equipment (IT) and the building cooling industries. Further, the information from the datacom equipment industry can vary by manufacturer and product level making for an infinite number of possibilities.
TC 9.9 includes representation from both of these industries and also the major datacom equipment manufacturers in order to bridge this information gap and provide an unbiased set of information that is manufacturer and product independent.
In 2004, ASHRAE TC9.9 published the book, Thermal Guidelines for Data Processing Environments. Its foreword states:
- Recent trends toward increased equipment power density in data centers can result in significant thermal design and operation issues, with the potentially undesirable side effects of decreased equipment availability, wasted floor space, and inefficient cooling system operation.
- There is often a mismatch of IT equipment environmental requirements with adjacent equipment requirements or with facility operating conditions and, thus, a strong need to find common solutions and standard practices that facilitate IT equipment interchangeability while preserving industry innovation.
- Thermal Guidelines for Data Processing Environments, authored by ASHRAE TC 9.9, provides a framework for improved alignment between IT equipment manufacturers (including manufacturers of computers, servers, and storage products), data center designers, and facility operators and managers.
- This guide covers four primary areas: equipment operating environment specifications (four classes are defined), facility temperature and humidity measurement (to evaluate data center health), equipment placement and airflow patterns (a hot aisle/cold aisle layout is recommended), and equipment manufacturers' heat load and airflow requirements reporting.
The people that participated in creating the thermal guidelines book include ANCIS, APC, Ceyba, Cisco Systems, CRS Industries, Cray, Data-Aire, DLB Associates Consulting Engineers, Echelon Corporation, EMC Corporation, Engineered Refrigeration Systems, Flomerics, Fujitsu Computer Systems, Hellmer & Medved Consulting Engineers, Hitachi, Hewlett-Packard, IBM Corporation, Innovative Research, Intel Corporation, Lawrence Berkeley National Labs, Liebert Corporation, Lucent Technologies, Mallory & Evans, Motorola, NCR Corporation, Sun Microsystems, Telcordia Technologies, Unisys, and The Uptime Institute.
Knowing the shortage of pertinent technical material concerning cooling of datacom equipment, TC 9.9 has been very active, focused on quickly compensating for that shortage. In addition to the book just mentioned, another publication addressing datacom equipment power trends and cooling applications is soon to be released. Also, the Chapter 17 of the ASHRAE Handbook - Applications has been rewritten for future publication. Lastly, TC 9.9 and its members have been hosting a symposium at every ASHRAE summer and winter meeting as well as writing ASHRAE Journal articles.
A good source of information on the design of datacom facilities is the ASHRAE TC 9.9 website (www.tc99.ashraetcs.org). The remainder of this article will focus on connected datacom equipment vs. demand loads and how to apply the "thermal guidelines for data processing environments" to help with this reconciliation.
Establishing the Connected and Demand Load of Datacom Equipment
Lacking any effective published statistical data to establish demand loads, the industry has typically been left with using the datacom nameplate data to establish a baseline. The methodology used has varied but predominantly it has been based on establishing some sort of "demand factor" to apply against this baseline.The demand factors used have been based on experience, anecdotal published factors, or specifically measuring some or all of the existing equipment. As previously stated, a significant "refresh rate" (datacom equipment adds, moves, and changes) typically occurs, making even the most comprehensive measurement to establish demand factors simply a snapshot in time.
ASHRAE TC 9.9 has made great inroads in improving the reconciliation of datacom equipment nameplate data vs. actual measured or demand load. Thermal Guidelines for Data Processing Environments provides a sample thermal report for datacom equipment manufacturers to publish critical environmental data, including measured load, in a standardized way.
One of the challenges associated with datacom equipment is the significant variation in its overall configuration. For example, for a single piece of equipment, the variation in load from its minimally configured form to its fully configured form could be 50% or more.
The thermal report template in the guideline addresses this situation by requiring that the heat release (in Watts) be provided for three different configurations (minimum, typical, and full). The thermal report also requires identification of airflow pattern (e.g., front to back, bottom to top) and the airflow quantity in cfm. Requesting this thermal report for all datacom equipment provides the designer with valuable information and significantly takes the guesswork or inaccuracies out of the issue of nameplate vs. measured load.
Some would say that the datacom manufacturers have misled the designers by providing nameplate data that is overstated. However, this is unfair since nameplate data is regulatory based and is predominantly focused on safety and essentially has no focus on establishing design loads.
Some time ago, the datacom manufacturers recognized the need for providing environmental design information about their equipment. They initially formed a Thermal Management Consortium that produced a trend chart that was published by The Uptime Institute in 2000.
Subsequently, the datacom manufacturers became critical members on ASHRAE Technical Committee TC 9.9. Their membership and participation is significant since their input provides far more credibility and support for the thermal report as well as other critical aspects of the thermal guidelines book.
A good approach to obtaining accurate datacom equipment demand loads, instead of applying factors to nameplate values, is to obtain datacom equipment thermal reports. Since the refresh rate is often every two to four years, it is better to obtain the heat release information in order to provide a good basic understanding of the current loads (Day 1 build), but then to apply growth factors for planning the ultimate or final build. Forecasting the final build is a complete topic unto itself and is not addressed here. TC 9.9 has written a book on trends and is a great source for forecasting called Datacom Equipment Power Trends and Cooling Applications scheduled for imminent release through ASHRAE.

The Thermal Report vs. Nameplate
Figure 2 is an example of a manufacturer using the thermal report template. Figure 3 compares the nameplate data to the heat release data. This comparison shows that the actual load at its "minimum" configuration is about 40% of the load indicated on its nameplate and about 60% of the nameplate load at its "full" configuration. This example not only shows how much lower and more accurate the heat release numbers are, but also the variation in load of 40% to 60% simply by changing its configuration.Figure 4 is published information about some HP products and shows the difference as well. These figures show the importance of obtaining the heat release information.
Although numerous manufacturers have committed to use the thermal report template, typically they will be providing it with the next release of their equipment and/or documentation. In the meantime, a good approach is to request this heat release information from the manufacturers even if it is currently not in their formally published literature.
Establishing Demands at Datacom Equipment Room Level
Through the use of the ASHRAE thermal report, accurate information is established for individual pieces of equipment. For upgrading existing facilities or simply to establish legacy baselines, it is helpful to develop a reasonable characterization of the connected load vs. the measured load.For traditional commercial and institutional projects, this characterization is pretty straightforward: divide the measured load by the connected load described on the contract documents or some other source. As stated earlier, the challenge with datacom is the constantly changing occupancy load as well as active vs. inactive load.
There are different levels of effort and accuracy required to establish the occupancy rate and adjusted connected load. In many cases, the level of effort required to accurately quantify the occupancy and active/inactive state within each rack is not cost effective. A simplified approach is to visually establish occupancy at an equipment row level and use this as a diversity factor in the calculations.
Where possible, it is helpful to classify the loads and associated demand factors for the major equipment types/uses such as:
- Storage servers;
- Computer servers;
- Communication;
- Print servers; and
- Command and control servers.
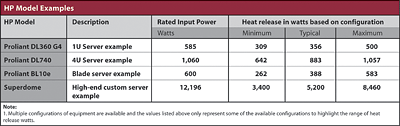
Final Thoughts
Designing a power and cooling infrastructure for its traditional 10- to 25-year life cycle, knowing that the datacom equipment it services has a typical lifecycle of two to four years, is a tough challenge; the risk of under-design or over-design is significant.There are no simple answers to addressing this challenge, but ASHRAE TC 9.9's work has made a positive contribution by developing the datacom equipment thermal report. This report provides a vehicle that the manufacturers can use to relay the actual heat release in watts for minimal, typical, and full configurations of equipment to other design professionals. Many of the major datacom equipment manufacturers serve on the committee and, therefore, the probability of manufacturers producing this report improves with each new cycle of equipment.
By requesting and obtaining the thermal report from the equipment manufacturers, the designer no longer has the risk of determining how to adjust the nameplate information to obtain the actual demand load for power and cooling. ES
EDITOR'S NOTE: Roger Schmidt of IBM and Christian Belady of HP (both are also members of ASHRAE TC 9.9) provided valuable information for this article including nameplate and heat release information about their products.