
When the San Antonio Spurs took to the court for its first preseason game this fall, it was in their brand-new, state-of-the-art arena. The groundbreaking ceremony for the Southwestern Bell Corporation (SBC) Center took place in August 2000, and this fast-track project was ready for the Spurs' first preseason game on October 18, 2002.
The SBC Center was designed to be a multipurpose sports and entertainment complex and is the home for the Spurs as well as the San Antonio Stock Show and Rodeo. The complex can seat 18,365 people for basketball games and about 17,000 for the rodeo. The 800,000-sq-ft facility can also host hockey games, ice shows, concerts, and numerous other events.
As can be imagined, a complex BAS is required for a structure housing these many diverse functions. With owners demanding a flexible and easy-to-use BAS, engineers pulled out all the stops to give them what they wanted in a very short time.
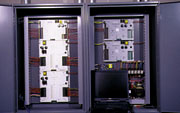
The criteria
The Spurs hired the AE firm of Ellerbe Becket (Kansas City, MO), to oversee much of the design and construction of the new arena. The firm was a natural choice, given that it had previously designed numerous other NBA/NHL facilities, including the Washington Wizards/Capitals' MCI Center and the Indiana Pacers' Conseco Fieldhouse.The BAS manufacturer chosen for the SBC Center was Automated Logic, whose local contractor, Alamo Controls (San Antonio, TX), engineered the hardware and software to perform the functions that Ellerbe Becket specified. Alamo Controls will also attend many events in the foreseeable future to ensure the BAS is working as specified.
What makes an NBA arena a little more challenging than other applications is that the functionality of the building changes from day to day. One day there might not be any events, the next day there might be a concert, and then the next day there might be a hockey game. Every different event requires the BAS to function in a different mode.
"An operator of an NBA facility requires a high degree of flexibility in the design of their controls systems," said Blake Ellis, principal, Ellerbe Becket. "Our goal is always to design a control system so they have the full ability to turn off and adjust setpoints for anything and everything because they all change. You cannot put in a local system on a time clock. It just won't work because it's not consistent from day to day."
In addition to flexibility, the owners were also interested in the ease of operation of the system. "The owners wanted graphic-based software because their system needed to be graphically configurable for the various events. If they're having a basketball event, they will graphically select the basketball mode, and it will change all their supply diffusers, their system setpoints, temperature and humidity control, outside air quantities, and everything else for the basketball event. All the supply diffusers are motorized, and they can be turned on and off," said Alfred G. Garza, P.E., project engineer, Alamo Controls Inc. (San Antonio, TX).
There is also a mode that is graphically configurable for the rodeo, another for a concert, and another one for an event that may just involve one quadrant of the arena. That last mode is set up such that the air will only be delivered to the parts of the arena that may be occupied. All told, there are currently seven preprogrammed modes, but the owners can add as many new modes as they choose.
The hockey mode is a little tricky, because it's necessary to control closely both the temperature and humidity down at the floor level, to control the quality of the ice during a game. It's a considerably different temperature and humidity control scheme than the basketball mode, where air should be blowing over the court, whereas during a hockey game, there shouldn't be any air blowing over the ice surface.
The rodeo mode is interesting as well, and this is the first time Ellis had to design a system around this type of event. "The rodeo is in February, so we run it in a mode called pyrotechnic mode, which is the mode typically used for events that require a lot of motors and engines. In essence, you run the system in smoke control mode, except we're cooling the air. The system actually runs in full exhaust mode, and that's how you cut down and control the dust," notes Ellis.
The air from the rodeo is discharged completely to the outside and none of it is returned to the arena. The ventilation rates are pretty high during the rodeo, but the air handlers can provide 360,000 cfm to the seating bowl alone. There are a total of 26 air handlers installed to handle the supply air with a total capacity of 682,670 cfm. As for the rest of the HVAC system, three chillers, at 950 tons each, are housed in the chiller plant, while the boiler plant contains four boilers at 7-MBtu output each.
Smoke control issues
One of the systems not controlled by the arena's BAS is the lighting, which is controlled by a separate, very specialized system. For anyone who has been to a sporting event lately, it's easy to understand why. The lighting control system needs to be able to turn banks of lights on and off very quickly, as well as turn spotlights on and off when introducing players before a game. Essentially, sports lights have a lot of strict requirements, which is why a separate system is needed.The smoke control system, however, is controlled by the BAS, although it, too, is rather complicated. "The smoke control system is complex because it has nine zones. This is the least number of zones we could have. The complexity of the system is driven, in part, by the approval process. Basically, the city and fire department had to understand what they were going to be getting before we got to the end of the project, to ensure it met their expectations," said Ellis.
Alamo Controls provided two hard-wired graphical firefighter's interface panels. One of the panels is located outside the building and the other panel is located in the security office, which is manned 24/7.
"There's a panel that depicts the entire arena and all levels of the arena. The firefighter has switches that are throughout his panel where he can turn on the smoke evacuation in any one area or in multiple areas. He has a host of switches through which he can manipulate the smoke throughout the arena. Since there's a panel in two different areas, he has two different control levels he can go to and still manage the smoke throughout the arena," said Garza.
The switching action allows the firefighter to configure the fan and smoke damper operation for the override and smoke management of the system. In addition, the firefighter has to be able to manage the smoke from all the pyrotechnic events that take place. Just think about all the fireworks that are set off at rock concerts and sporting events. It's up to the firefighter to immediately rid the arena of the smoke and get the system back into normal operation.
In the first smoke control zone, which encompasses the seating bowl, two exhaust fans in each quadrant were installed in order to exhaust 580,000 cfm of air. "Two bowl air-handling units and one concourse air-handling unit per quadrant provide the makeup air, bringing in 100% outside air for 520,000 cfm total. The remainder is infiltrated through the exterior walls and doors," said Ellis.
The upper and lower concourses are zoned by quadrant and by level, which allows the fire department to exhaust only a small area of the concourse. The smoke control system is interlocked with the fire alarm system, with all the control being done by the HVAC system.
"Because the control system is so complex (e.g., many dampers that need to be activated, many different fans that need to be turned on and off), and we had nine different possible options that we could be under, it was far more cost effective to provide a UL-listed smoke control system than expand the fire alarm system to control HVAC equipment in a fire mode. You would still then have to have the HVAC control system in normal mode," noted Ellis.
The grand finale
For a system this large, one may think there were some interoperability issues that arose between the BAS and the various HVAC components during the project. According to Garza, though, that wasn't the case. "Everything was handled with BACnet, and it was trouble-free," he said.The York chillers were provided with BACnet through Web portals, which brought their information directly into the software via the Ethernet. The boiler manufacturer (PVI) was also contracted up front to provide BACnet control devices that were seamless. Garza noted that the smoke control interface between Automated Logic and Simplex was also seamless. "There was a lot of interoperability, and it was really very seamless using the BACnet system. The start-up on this project was one of the least concerning items that we had," he said.
While both Ellis and Garza noted that the project went very smoothly, they also admit to challenges. For Ellis, the most challenging part of the design involved the smoke control system. "The system is about twice as big as what we've done before in terms of quantity of air that's being exhausted. The reason why is there was a lot of concern as to the amount of combustibles that would be located on the floor of the arena, but not in a mode where you actually had an event."
Such an event could include a home show, for example, where an entire log home might be built on the arena floor. If that house were to catch on fire, the system would need to be able to respond appropriately. "There were many discussions about what size of fire needed to be modeled, and the size of fire that was modeled here was very large. Then if the fire is large, it produces a large amount of smoke, then our exhaust rate is driven by that, based on how much smoke was removed. It was challenging," said Ellis.
For Garza, the biggest challenge was the short amount of time in which the system needed to be finished, as well as all the coordination that needed to take place between all the trades in that short period of time. "Fortunately, the general contractor recognized early on that this was going to be a real coordination nightmare. He set up weekly meetings between our project engineer and all the parties - electricians, mechanical, sheet metal, piping, including the fire marshal. We had all these people meeting every week for probably the last six months straight," said Garza.
The end result is a building - and a BAS - that was finished on time and should serve San Antonio well for years to come. ES