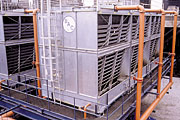
Some of these choices include making sure the tower is sized correctly to begin with, incorporating better fans, including variable-frequency drives (vfd's), adding new or more efficient fill, or using a new set of nozzles to give better distribution over the fill. But it's important to remember that a cooling tower works as a system: Adding an oddball combination of components might not solve a problem, and indeed, it could make existing problems worse.
Ignored and Undersized
Many believe that cooling towers play a rather minor role in an application's direct energy consumption. Maybe that's because they are relatively inexpensive pieces of equipment, or perhaps because it's perceived that they'll last forever even without much maintenance. However, a cooling tower's relationship with the chiller(s) has a large indirect effect on energy savings because the efficiency of a chiller improves with colder condensing water, which the cooling tower provides.That's very important today, given that energy prices are ratcheting upwards every day - it pays to look at every component in a system to make sure that each one is saving as much energy as possible. With cooling towers, the water should be as cool as possible when returning to the chiller.
"The chiller probably uses five times as much energy as the cooling tower, which is why the focus is always on the chiller," says Russ Lindemann, cooling tower product manager, Baltimore Aircoil (Baltimore). "But for every degree cooler a cooling tower can make the supply water going to the chiller, it is estimated that the chiller energy efficiency will increase 2%."
Older towers have a tendency to be less efficient, and they can use two to five times as much energy as a newer cooling tower. The inefficiencies may be tied to old designs that used inefficient air moving systems, fill systems, or just limited designs.
"Older towers may also suffer from degradation due to age. The fill material inside the tower may be damaged, partially clogged, or have biological growth that limit the mass transfer or cooling capability of the tower. An inefficient tower can often be replaced with a payback period of less than two years," notes John Flaherty, president, Delta Cooling Towers (Fairfield, NJ).
Another reason why a cooling tower may be inefficient is that it was not sized properly from the beginning. "The cooling tower is the cheapest surface in the plant, yet everybody skimps on it. That doesn't make any sense to me," says Richard DesJardins, owner, DesJardins and Associates (Palm Desert, CA). "Colder water provides a much better savings by allowing the compressor or other equipment to operate more efficiently. It makes sense to use a bigger tower that provides colder water, even if the power used remains the same."
DesJardins notes that the cooling tower is the one component in the system that should be oversized, yet it never is. That's because it always comes down to the bottom line - if one engineer specifies a larger cooling tower that costs more, he may lose the job. "So everybody goes in and trims the price a little bit. An owner may always have problems with his system, but never enough to really shut down. The system will just barely work," notes DesJardins.
Specifying the Right Tower
If it is decided that the existing cooling tower is too small or too old and needs to be replaced, engineers should make sure the tower they've specified will work correctly for a particular application. (See sidebar, "Five questions that need to be asked when selecting a cooling tower.") One way to do that is to make sure the specification is very detailed - and that includes performing a power evaluation."You can tell a manufacturer that you want low horsepower, as well as fill that doesn't plug. Also include a power evaluation, which states how much power is worth to the owner. While the manufacturer may not have exactly what you're looking for, chances are that someone will come close," says DesJardins.
It's also important to make sure you get the tower you specify, which is where the Cooling Technology Institute (CTI) will help. Too often in the past, a cooling tower would be specified, and its thermal performance would not be what the manufacturer promised. Now manufacturers can have their cooling towers certified to ensure that a cooling tower will give the condensing water temperature that was originally specified.
DesJardins is adamant that any cooling tower specification should call for a field test or "CTI certification" that calls for the manufacturer to have had its tower tested to the claimed capability by a licensed CTI tower testing company. The manufacturer of a CTI-certified tower line should also demonstrate they have a viable rating system to predict performance at various operating conditions.
"All manufacturers have CTI certification available to them," says Lindemann. "Having a CTI-certified product in and of itself gives some assurance to the engineers and owners that the equipment is going to perform to a certain level or a certain efficiency. Basically it's a guarantee that when you say the cooling tower is going to provide 85?F condenser water temperature that you will get 85? condenser water temperature."
The only other way to make sure a cooling tower is performing as specified is to do a thermal performance test. Given that these sometimes cost $4,000 and up, it's probably better to specify a CTI-certified tower in the first place.
Fans, Fill, and Nozzles
It usually makes sense to bring the existing tower to its fullest potential, which may involve extensive renovation. That can include changing to new fill that has better heat transfer characteristics, adding fan power, changing fan sizes, opening up the air inlets, changing nozzles, etc.As DesJardins notes, "If the structure is still good, it is usually best to try to save the old tower rather than build a new one simply for tax considerations - repairs can be expensed, while new towers need to be written off over a longer period of time."
The fans are the number-one user of power in a cooling tower, and that's the first place to look for energy savings. Engineers may want to consider two-speed motors, as they use about 1/6 of the power at low speed.
It's also possible to use vfd controllers for the fans and pumps in order to reduce the parasitic power at low heat loads. There is an advantage because fan power varies as the cube of the air rate (cfm), and thermal performance varies directly as the air rate.
"There are sometimes limits on this type of operation when using propeller fans that often have critical speeds where they should not operate in order to not self-destruct (the natural frequency of the blades acts like a crystal glass that shatters). Also, if you are lowering the water rate in cold weather, you could get to a very low gpm/sq-ft level that promotes ice formation in the fill or a portion of the fill," says DesJardins.
If it is deemed possible to include two-speed fan motors, most cooling tower manufacturers are happy to oblige. Baltimore Aircoil, for example, offers its "Energy-Miser" fan system. "With the Energy-Miser, you can operate the full-size fan motor for roughly 20% of the time, and you can use the lower horsepower motor for the other 80% of the year to provide significant operating cost savings," says Lindemann.
It may also be possible to increase a cooling tower's fan efficiency, if there is room for a bigger diameter fan. Unfortunately, this may not be economically feasible, because it requires changing not only the fan, but the fan support, the fan cylinder, fan guards, drive shaft, lubrication lines, etc.
"Sometimes the fan cylinder can be changed to one with a better aerodynamic shape or by adding a velocity recovery stack on top of the existing cylinder," says DesJardins. "These changes may increase the air flow and require fan changes to lower the fan pitch to return to the original airflow rate at a lower power consumption in order to avoid excessive drift."
Another key point as far as fans are concerned is location, location, location. Many towers are designed with squirrel cage blower fans rather than propeller fans. These types of fans usually use more power; however, they are often used because the tower is located indoors or in an enclosure. The blower fans will work better with the resulting higher inlet or discharge air pressure losses. Locating a tower outside or in the open so propeller fan towers can be used will likely reduce the required fan power.
The fill is another component that can help save some energy as well. Many old towers have splash-type fill, which is not as energy efficient. If the system is not normally subject to water scaling, algae, or other contamination, some towers may benefit from a change to film-type fill. (In some cases the more modern film-type fills can plug due to water contamination from algae, dirt, minerals, etc. Aftermarket companies such as Lantec Products, Brentwood Industries, and Tower Components, Inc. have been developing fills that should help to minimize these problems.) If this is done, it is necessary to consider all of the parts of the tower - especially the fan and nozzle systems.
As for the nozzles, in a crossflow tower, it is important that the nozzles properly distribute the water over the fill. Better distribution can usually only be obtained by adding distribution decks directly below the nozzles; however, in a counterflow tower the nozzles can contribute as much as 25% of the cooling, and changes to the nozzles can either help or hurt.
"Some towers are designed for high pressure, very fine spray nozzles that give a lot of cooling at the expense of a high nozzle pressure that requires more pumping power. For a small tower this is not usually considered important, but larger towers probably should be evaluated for power costs," says DesJardins.
Some manufacturers use large diameter orifice nozzles with various types of splash diffusers to get very even water distribution over the fill with lower pump heads, resulting in less required power. However, changing to lower pressure nozzles may take away from the thermal capacity of the tower - or it may give better performance if it improves the distribution of water over the fill by replacing hollow cone high-pressure nozzles with full cone or full coverage nozzles.
"If the existing nozzles are not giving good water distribution, then a change may be justified," says DesJardins. "Maybe the water flow rate has changed from the original design - changes to the orifice diameter may be all that is needed to get back to good performance."
As with any of the renovations discussed here, the selection of the nozzle for a given fill should always be made by someone knowledgeable on the overall effect of the change on thermal performance. Thermal performance capability is not predictable without testing a given nozzle with a given fill - guessing or 'mix and match' decisions can cause significant problems. Engineers should always contact a cooling tower manufacturer or cooling tower consultant to make sure that they're specifying the correct components for a particular tower. ES