
The required space for all the equipment must be discussed with the project's space planner. Accessibility for maintenance and repair must be considered with the client at this time.
Plans and specifications are then developed into construction documents that contain the design intent, system layout, equipment descriptions, and component details. The schematic diagram is a simple communication tool to convey the design intent of the pumping system. The communication is directed toward the client, the design team, the code authority, the contractor, and the historical record of the project. The system layout is then transformed on to floor plans and elevations. The equipment schedules, specifications, and details complete the construction document package.
Where To Start
The design of building HVAC systems is similar to assembling a puzzle without knowing exactly what the final picture is supposed to look like. It is an iterative process involving many steps, including calculating the building heating and air conditioning loads, defining space requirements for mechanical equipment, specifying and selecting the mechanical system components, coordinating with other disciplines, and creating the construction drawings and specifications. All of this is done while keeping the building design and construction budget in mind.
One very important piece of the mechanical system puzzle is the HVAC pump. Pumps circulate a heat transfer fluid, normally water or a glycol-water solution, from heat source to heat sink. The two most common types of centrifugal pumps used in heating and cooling systems are in-line pumps and base-mounted pumps, with the end-suction style being the most used type of base-mounted pump. The advantages and disadvantages to each type are outside the scope of this article. Once the design requirements are determined for the pump, the process of selecting a HVAC pump is relatively straightforward. Consideration for primary pumping, primary-secondary pumping, parallel pumping, series pumping, etc., and pumping arrangement such as direct return, reverse return, or a combination of both, is defined by the schematic diagrams.

Flow Diagams
The first step in documenting pumping systems is the development of schematic diagrams for the heating and cooling systems. Schematic diagrams are important in that they establish the relationships between the heating and cooling equipment, the pump(s), and the terminal heat transfer devices that they serve. The schematic diagrams also establish the system piping configuration and the location of valves, air control devices, and other piping specialties. The schematic diagrams should be started early in the design development phase and developed further as the system design progresses.Equipment Room Floor Plan Layout
It is important to ensure that enough space in the building mechanical room is allocated for the installation of HVAC pumps and associated piping. Adequate space allocation not only provides room for proper installation but also allows for adequate maintenance space at the pumping station, while not wasting valuable building floor space. In-line pump installations are simpler than base-mounted pumps; however, in both cases improper installation can lead to premature failure of the pump, which can be difficult and costly to rectify.Although it is desirable to locate the pumps in close proximity to the equipment (e.g., boiler or chiller) that they serve, this may not always be feasible. Heating water pumps are located so that the heating source is on the suction side of the pump; water is drawn through the boiler. This pump arrangement is to facilitate the removal of air from the system. Chilled water pumps are located so that the chiller is on the discharge side of the pump; water is pumped through the chiller. This location is selected to obtain dependable flow at the flow switch on the chiller discharge.
Most pump manufacturers now provide CAD templates for their equipment. These are available from software loaded onto local computer workstations or as downloads from the manufacturer's website. The pump templates can be placed in the building floor plans as a starting point for designing the pumping station.
Once the pump(s) is located on the floor plan, the housekeeping pad or inertia base is indicated. In multiple pump installations, leave at least 24 in. of clearance space between and around the housekeeping pads for pump maintenance. This is especially important in large pump installations, where the pump motors can be 20 hp or larger. In the event of a motor failure, access to the pump motor for removal and replacement will be required by the building maintenance personnel. Consider a lifting hook or rail above in-line pumps to aid in their removal for service.
Consideration must be given to defining pipe supports. Pipe hangers are often a mixture of a constant type and a spring type. The spring type is used at the high point of the vertical rise off the pump discharge, which compensates for the vertical expansion as the pump starts operation. Pipe hangers that support large diameter pipes require structural coordination to carry the load. Pipes are also supported off the floor at or near the pump connector device. Support in these locations requires coordination with the pump's base pad. Pumps and pipings located in earthquake zones require special seismic restraints.
It is important to keep in mind that the floor plans should be kept simple and information should be shown only as often as needed, preferably once. For instance, individual piping specialties such as valves, control objects, and instrumentation need not be shown on the floor plans. These items are shown on the schematic diagrams and in the equipment details. Equipment nomenclature and pipe sizing are shown on the floor plans and schematic diagrams, but not in the equipment details. Motor horsepower information need only be shown in the pump schedules.
Pump Details
Equipment installation details are an important part of the construction documents. In the case of HVAC pumps, they not only indicate the type of pumps required but the details are also a useful tool for the designer, to double-check floor plans and piping schematics. Figure 1 is a typical equipment detail for the installation of an in-line centrifugal pump. Figure 2 is a typical equipment detail for a base-mounted, end-suction centrifugal pump.In-line pump installations are relatively straightforward. A shutoff valve is located on the supply side; a check valve and a combination shut-off/balancing valve is provided on the discharge. In-line pumps are supported independently from the piping system for vibration isolation, and to keep the pump flanges from being over-stressed.
Arguably, the most important aspect of the base-mounted pump installation is ensuring uniform flow into the pump impeller. A minimum of five diameters of straight pipe and long radius pipe elbows should be provided at the pump inlet. If floor space is at a premium, pump manufacturers recommend a suction diffuser in lieu of the section of straight piping. Contractors may offer this as a value-engineering alternative as well, because it eliminates the need for a separate strainer upstream of the pump inlet.
The pump should be provided with a shut-off valve on the supply side. A check valve and a combination shut-off/balancing valve are provided on the discharge. Allowing 10 pipe diameters between the pump discharge and the balancing valve ensures the uniform flow that is needed for accurate balancing.
Base-mounted end suction pumps should be installed on a housekeeping pad. Housekeeping pads keep the pump off the mechanical room floor, and provide a secure surface for anchoring the pump and motor frame. Housekeeping pads are normally 4 in. high, a minimum of 6 in. wider on each side of the pump, and two to three times the weight of the pump. The inertia base for vibration isolation is used only when the pump is located in a mechanical room that is not on grade, or in applications where vibration isolation is critical, such as in a performing arts center or semi-conductor manufacturing facility.
The pump is isolated from the piping system by braided flexible piping connectors or bellows-type vibration isolation fittings to prevent equipment vibration from being transmitted through the piping system to other areas of the building. Finally, since the inlet of and outlet of the pump volute is not necessarily the same size as the distribution piping, eccentric reducers are needed on the pump inlet and concentric reducers are used on the outlet.
Pump Schedules
Equipment schedules are included within the construction documents in order to indicate to the contractor the correct HVAC equipment to provide. Figure 3 is a typical HVAC pump schedule that would be included in the construction documents. It is important to ensure that pumps listed in the schedules agree with the requirements listed in the specifications.The pump tag is the equipment number assigned to each pump, for instance CHWP-1 for chilled water pump #1. The location indicated in the second column may be either the number assigned to that specific room, or a verbal description of the pump location. The specific system that the pump serves is indicated in the third column. This could be chilled water, heated water, condenser water, or a similar description. The pump type is the specific style of pump required, such as in-line or end-suction.
The design pump data is shown in the next three columns. This is the calculated design heat transfer fluid flow, the calculated system pressure loss, and the pump efficiency indicated by the pump curve or selection software. The information in these columns should indicate operation near the pump's best efficiency point (BEP). A pump manufacturer may produce several models of a specific style of pump that will meet the design requirements. The column titled "Head @ 115% capacity" helps to ensure that the selected pump can operate in the preferred operating range (between 70% to 120% of the BEP) without a significant drop off in efficiency.
Specifying the motor horsepower (hp) and speed (rpm) indicates the pump's electrical requirements. The electrical service requirements (voltage/phase/frequency) are the responsibility of electrical contractor, but this information needs to be coordinated with the electrical engineer during the design phase. The mechanical contractor is responsible for supplying a pump that meets the specific motor requirements indicated on the electrical plans. If the pump is to be supplied with a VSD, that is indicated here as well.
The casing sizes are the pump's suction and discharge sizes, not the pipe size connected to it. Recall from Figure 1 that reducers are normally provided at the pump inlet and outlet to transition to the size of the connected piping.
If it features a concrete inertia base or other type, vibration isolation is needed. It is shown in the schedule as well. The nomenclature of the specific type of vibration isolation needed should be coordinated with the mechanical specifications. The deflection is a function of the application, building construction, and style of isolator used. For base-mounted pumps that do not require inertia bases, the schedule should indicate N/A for "not applicable."
The last column is used to indicate the pump used as the basis for the system design. Indicating a specific manufacturer and model number does not limit competition, as the specifications usually allow multiple alternatives, however, it does give the contractor a better idea of the required pump(s). In addition, this column may also refer to notes at the end of the schedule if needed. Typical notes would be to indicate if a water-glycol solution is used for the heat transfer fluid or if the pumps are to run in series, parallel, or simply as operating/standby.
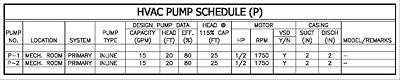
Design Checklist
It is important that the HVAC system designer complete a design checklist to ensure the pumps are properly indicated in the construction documents and coordinated with other disciplines. The following is a suggested checklist for HVAC pump design documentation.- HVAC pumps are located on building floor plan.
- Pump nomenclature agrees on floor plan, schematic diagrams, and equipment schedule.
- VSDs are located on floor plan and coordinated with electrical engineer.
- Electrical requirements for motor hp are coordinated with electrical engineer.
- Housekeeping pads are shown on floor plans, and coordinated with architect.
- Equipment weights, housekeeping pads, and inertia bases are coordinated with the structural engineer.
- Floor drains are located near HVAC pumps and should be coordinated with plumbing engineer.
- Pumps are connected to correct piping system.
- Pump details are referenced on floor plans.
- Piping specialties shown on schematic diagram agree with pump details.
- Water flow rate and piping head loss calculations are recorded in project folder.
- Pump selections and catalog information is included in the project folder.
- Pumps are properly scheduled, including all relative notes, and coordinated with project specifications.
Conclusion
The design of building HVAC systems is a complicated process, involving many steps. Not the least of these is the proper selection and documentation of the HVAC pumping system. Complete documentation of the pumping systems includes a schematic diagram, floor plans, pump installation details, and equipment schedules. All of these must be coordinated to avoid inconsistencies in the documentation. Adequate floor space must be provided for the pumps to allow for the required piping connections and service areas for maintenance.Details of all types of pump installations are also required. The selected pumps must also be coordinated with the project architect, structural engineer, and electrical engineer. Following these guidelines will help to ensure that the installing contractor and maintenance personnel fully understand the centrifugal pump's function in making the building mechanical system achieve its design criteria. ES