There are many misconceptions around achieving highly efficient operation from hydronic condensing boiler systems. The reality is, various factors will influence the operational efficiency of boiler plants. In this article, system considerations, boiler applications, and combustion control functionality are discussed for realizing energy savings.
The main factor system designers, end users, and operators can directly influence that will affect boiler efficiency is the return water temperature. Lower return water temperatures will result in more condensing operation. Since condensing occurs when latent heat is extracted from the flue gases, whenever condensing is happening, boiler plants operate at higher combustion efficiencies. One way to address return water temperatures is by adjusting supply water temperatures — if supply temperatures are lower, that will naturally result in lower return water temperatures. In systems requiring higher supply water temperatures on design days/hours, outdoor temperature reset can be utilized for the remainder of the operating hours. Outdoor result functionality includes a temperature sensor installed outdoors that lets the boiler system know as outdoor temperatures rise. Since heating loads generally vary inversely with outdoor temperature, the boiler plant responds to these higher outdoor temperatures by lowering the heating water set point, thereby reducing the return water temperature and increasing efficiency. Another way of reducing return water temperatures is by designing and selecting systems and coils with a larger difference between the entering and leaving water temperature (∆T). In addition, this approach results in lower flow rates, reduced pumping requirements, and potentially smaller pipe diameters, resulting in lower operating and capital costs.
During the combustion process, thermal energy is available to transfer to the hydronic heating system in two forms. Chemically, the products of combustion are primarily CO2, H2O in gaseous form, and a certain percentage of excess air to ensure clean combustion. Sensible heat accounts for most of the heat available and has been used to transfer heat into the hydronic heating system in legacy noncondensing products. Legacy boiler designs were limited to noncondensing, as the product design and materials could not survive sustained condensing operation. In these designs, as much sensible heat as possible is extracted from the flue gases, and then they are generally expelled from the building via vent systems. However, there is additional heat available in these flue gases trapped in the form of latent heat — heat that can be extracted during the phase change from vapor to liquid, which is referred to as condensing. Condensing of the flue gases occurs when they come into contact with temperatures lower than their dew point temperature. When return water temperatures are below that dew point temperature, condensing occurs, and even lower return water temperatures increase the amount of condensing occurring. Modern boilers, such as the ones shown in Figure 1, are capable of handling continuous condensing operation and taking advantage of the increased efficiency resulting from harvesting both sensible and latent heat from the flue gases.
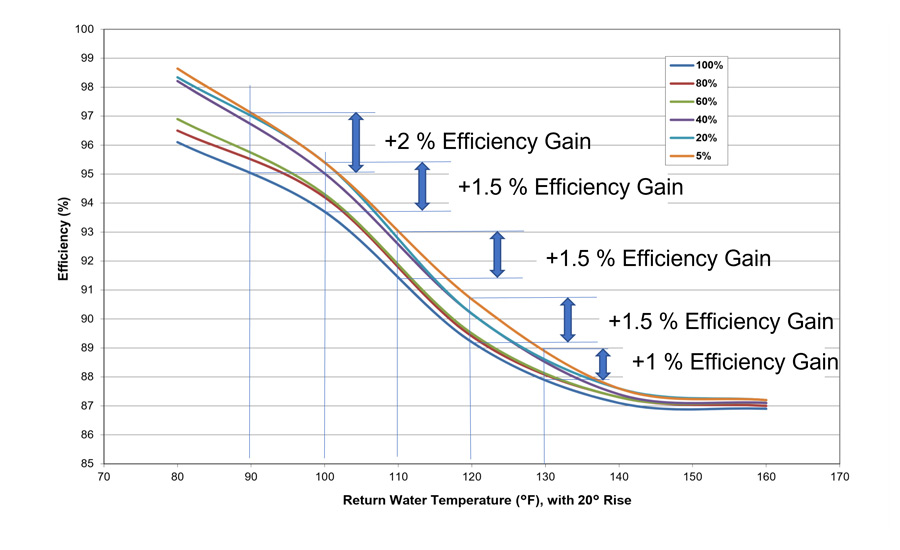
In all heat transfer applications, a larger heat transfer surface area generally results in greater heat transferred and, therefore, more efficient operation. Hydronic boilers are no different. However, a larger heat transfer surface area results in more materials and space and, therefore, cost, so balancing these factors against one another is critical. One way to take advantage of available heat transfer surface area in boilers is to reduce blower speeds and firing rates, referred to as turndown. Turndown is expressed as the inverse of the minimum available firing rate — for example, a 20:1 turndown boiler is capable of firing at 1/20, or 5%, of its rated maximum. As a result of having 20 times the amount of heat transfer surface area available as is necessary, when a boiler is firing at 5%, it will operate significantly more efficiently at that firing rate. This increase in efficiency is typically between 1%-2% in absolute efficiency gain, even with relatively small ∆T, as shown in Figure 2.
For this reason, it is highly recommended that multiple high-turndown boilers be used in most applications to maximize operational efficiency. Additionally, the controls sequence should take advantage of running as many boilers at once at as low a firing rate as possible. It is not recommended to keep boilers in standby whenever it’s possible to have them run at a low firing rate. These recommendations are only valid when proper combustion control at high turndown is implemented.
Most equipment is designed, tested, and rated at the maximum operating point, and, therefore, there are special considerations when they are utilized at some part-load or minimum conditions. For boilers at high turndown, excess air can cause reductions in efficiency. Excess air is simply the amount of air entering the boiler that is more than necessary for combustion. A small amount of excess air is typical to maintain flame stability, but as the amount of excess air increases, the dew point temperature of the resulting flue gases decreases. This results in lower required return water temperatures before condensing begins and less efficient boiler operation. The best solution for properly controlling excess air in high turndown systems is the use of continuous oxygen trim. Oxygen trim systems utilize an oxygen sensor installed in the unit that is constantly measuring the amount of oxygen left over after combustion. Perfect combustion would result in zero oxygen remaining, but due to the aforementioned flame stability issues, optimal combustion accounts for having some remaining oxygen. Ideally, a continuous oxygen trim system reacts to the oxygen levels after combustion by making incremental changes to independent air and fuel valves while the boiler continues to modulate the firing rate and blower speed to maintain temperature set points. This results in a boiler that is capable of properly modulating combustion throughout the firing range as well as reacting to seasonal variability and changing properties of incoming combustion air. These continuous oxygen trim systems are capable of significantly increasing the dew point temperature of the flue gases to maximize condensing operation. An added benefit of continuous oxygen trim is that it also serves as an early warning sign of other combustion issues, such as flue gas recirculation or contamination.
As systems and equipment continue to strive for greater operational efficiency and energy savings, a greater number of factors influence those objectives. Several critical steps have been identified in this article for realizing efficient condensing operation. Designing hydronic boiler systems and coils with return water temperature in mind and taking advantage of outdoor temperature reset are important selection parameters that determine how much condensing will be possible. Utilizing high-turndown equipment and implementing controls strategies to use a larger surface area increases the heat transfer efficiency of the boilers. Finally, performing high turndown correctly coupled with continuous oxygen trim assists with ensuring proper combustion at all loads and conditions. When applied properly, all of these hydronic boiler system strategies combined will result in increased efficiency and lower energy costs.