Our industry has traditionally relied heavily on fossil fuels, including natural gas, to provide heating and hot water for commercial buildings. It is not unusual to go into a large commercial building (those with a gross area of more than 300,000 square feet) and find natural gas boilers that provide heating in a closed-loop hydronic system.
A typical alternative to gas-fired boilers is the use of electric reheat coils. Electric reheat works by using electric resistance coils that directly heat the air that is supplied to a room. One of the benefits of electric reheat is its simplicity. Electric-resistance heaters are relatively easy to install, control and maintain. Since they do not require any additional fuel sources or piping, they reduce the overall installed cost of the system.
A potential issue with using electric reheat in terminal units is that it can create thermal comfort issues if not properly designed and maintained. This could happen when using electric reheat that has staged control and not silicon control rectifier (SCR) control. A terminal unit discharging air at 100oF will most likely cause air stratification issues causing the hot air to stay above the occupied zone and not be felt by the occupants. This impacts the occupants and is an unnecessary waste of energy.
Another issue with using electric reheat is that it can be very expensive to operate. This is because the coefficient of performance of an electric heating coil is at most 1; meaning for every Btu per hour of energy input into the coil, one can use, at most, 1 Btu per hour output energy to heat the air that is being delivered into an occupied space.
As building owners and designers become more aware of the long-term environmental impact of using fossil fuels to heat buildings, there has been an openness to embrace electrification in tandem with the pursuit of cleaner sources of energy. Accordingly, state and federal initiatives have spurred new interests in incorporating highly energy-efficient heat pumps into a building’s HVAC system.
In their most basic form, heat pumps are mechanical devices that can extract heat from one location and transfer it to another location. Both air- and water-cooled heat pumps operate on the same basic principle. A heat pump consists of an evaporator coil, a condenser coil, a compressor, an expansion valve, a four-way valve, and refrigerant. The evaporator coil is used to extract heat while the condenser coil is used to reject heat. While operating on the same refrigerant cycle as a standard air conditioner, the use of a four-way valve allows heat pumps to provide cooling or heating.
A compressor is used to provide the pressure (head) required for the refrigerant to flow through the system as well as compress the refrigerant to a high temperature, sometimes a superheated state before it enters the condenser coil.
The expansion of a throttling valve in the heat pump helps to regulate the flow of refrigerant and ensure that the system operates efficiently and effectively. Its main function is to reduce the pressure of the refrigerant that has been compressed in the condenser coil and turn it into a low-pressure, low-temperature liquid that can evaporate and absorb heat in the evaporator coil.
Figure 1 shows the flow of heat (thermal energy) of an air-cooled heat pump that is operating in cooling mode. The coil located inside of the space that calls for cooling becomes the evaporator coil; the refrigerant that flows through the coil to absorb energy from the space. The energy is then conveyed by the refrigerant to the condenser coil, where it is rejected to the outdoors. Both the evaporator and condenser coils typically operate with dedicated circulation fans. This type of heat pump is called air-cooled because the heat from the indoor space (and the heat generated by the refrigerant compressor) is rejected directly outdoors.
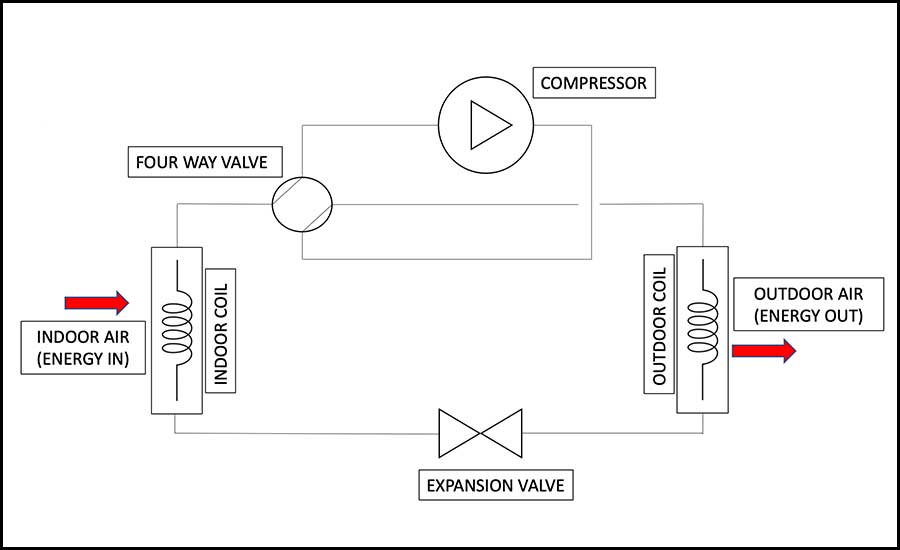
As shown in Figure 2, in heating mode, the two coils switch roles. The coil located indoors becomes the condenser coil and the coil located outdoors becomes the evaporator coil. As the refrigerant passes through the outdoor coil, it absorbs heat and evaporates into gas, which then releases its heat as it condenses back into a liquid at the indoor coil.
One of the drawbacks of using air-cooled heat pumps in colder climates is the buildup of ice on them when the heat pump operates in heating mode. The more ice builds up on the outdoor coil, the less heat the heat pump can absorb from the outdoors. To mitigate this issue, the onboard controls of the heat pump will activate a defrost cycle. During the defrost cycle, the heat pump will temporarily switch into a cooling mode to melt the ice buildup, and then switch back to heat mode, usually after approximately eight to 10 minutes. Care must be taken when locating heat pumps in colder climates to avoid the buildup of ice on any walkways near the building due to the water generated during the defrost cycle.
A widely used HVAC system that works based on the heat pump principle is the variable refrigerant flow (VRF) system. The VRF system incorporates an inverter into the compressor to allow variable compressor motor speeds. This allows for variable refrigerant flow instead of the conventional on-off flow found in typical systems. The amount of refrigerant can be zone controlled using a microprocessor receiving information about zones from sensors throughout the system. A VRF system looks only at the dry bulb temperature of the space and is limited to only heating and cooling the space, meaning they cannot perform dehumidification while also maintaining the dry bulb space temperature.
In order to not turn off the fan associated with the indoor coil during the defrost mode, the VRF system manufacturers have implemented various strategies, one of which is splitting the outdoor unit into multiple refrigerant circuits and having only one circuit at time go into the defrost mode. This ensures the VRF system can provide continuous heating, albeit at a reduced heating capacity.
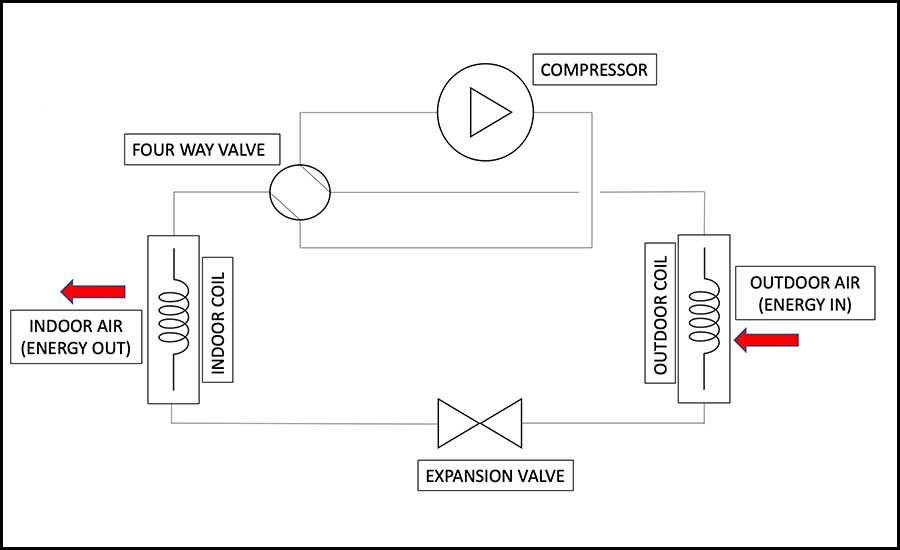
Figure 3 shows a diagram of a water-cooled heat pump system connected to a cooling tower system. The cooling tower system is responsible for removing heat from the water and releasing it into the atmosphere. From the perspective of energy and water conservation, there are a couple of drawbacks associated with using this type of system. First, the cooling towers operate by using evaporation to cool the water. This means that significant amounts of water are being lost out of the system continuously. Secondly, water that is circulated through the cooling tower must be treated to prevent the growth of bacteria and other microorganisms that can cause corrosion and fouling of the heat exchangers. This is typically done through the use of biocides, which kill bacteria, and corrosion inhibitors, which protect the metal surfaces of the system from corrosion. This treatment increases the complexity and cost of maintenance for the system. Lastly, in colder climates, a boiler system is typically needed to inject heat into the water system, which is then used by the water-cooled heat pumps to heat the spaces they serve. Typically, the boiler system uses dedicated gas-fired boilers, pumps, and heat exchangers (HXs). The dedicated HXs are needed to decouple the closed-loop boiler system from the open-loop cooling tower system.
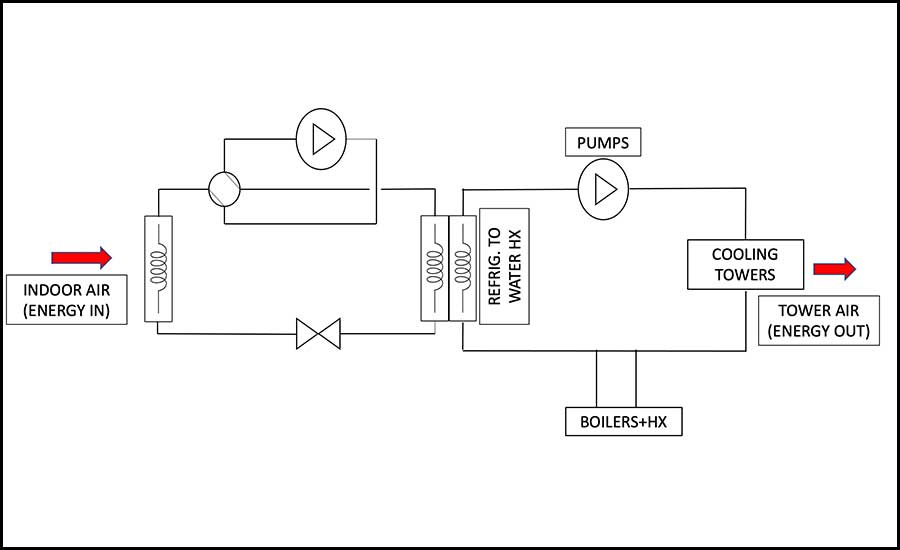
There are two types of geo-exchange systems: closed loop and open loop. Closed-loop systems use a series of underground pipes that are buried beneath the Earth’s surfaceand then circulate a water/antifreeze solution to transfer heat between the ground and the HVAC system. Closed-loop systems are the most common type of geo-exchange system. The process of creating boreholes involves the drilling of holes deep into the ground, typically several hundred feet, and installing a closed-loop pipe system that circulates the water to and from the building. Open-loop systems use groundwater from a well, a pond, or a local body of water as the heat transfer fluid.
Despite their relatively high initial costs, a geo-exchange heat pump system is currently considered the gold standard for decarbonization efforts due to their reliability, low operational costs, and low environmental footprint. Several factors such as the local climate, the geology of the site, available land, and costs are typically analyzed to determine the size of the geothermal field. As the system operates, rejecting heat to the ground during summers and extracting heat from the ground during winters, studies are required to determine the capability of the ground to perform as designed over years.
Figure 4 shows a diagram of water-cooled water-to-water heat pump system connected to a geothermal field. In this scenario, a dedicated water-to-water HX is used to decouple the building hydronic system from the geo-exchange loop. This provides added resiliency to the system by allowing the borefield system to be flushed without impact to the building loop water quality.
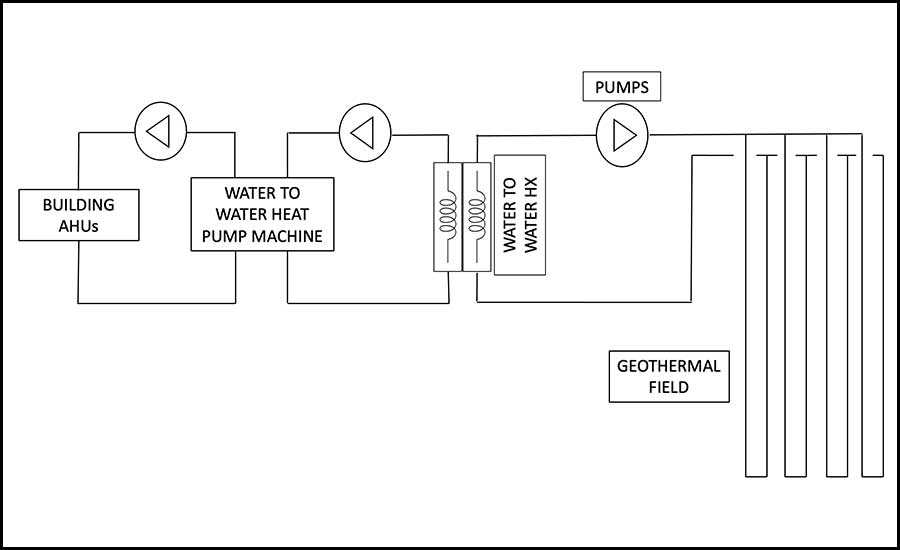
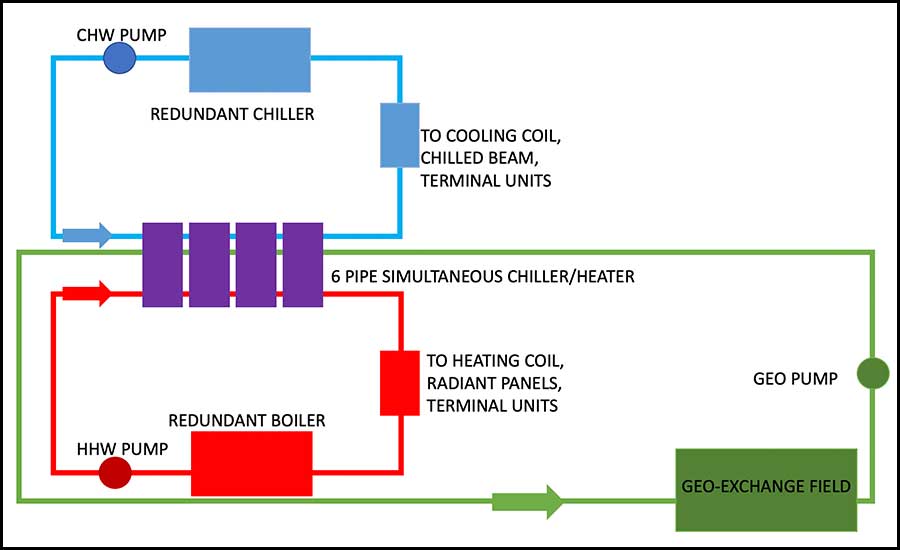
As electrification of buildings becomes more prevalent, the use of heat pumps will continue to increase. It is important for design engineers to consider financial, operational, and environmental feasibility when selecting the type of heat pump that will best suit a given project.