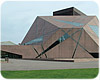
A
new frictionless chiller, VFDs, and energy management system has
saved the McNamara Alumni Center at the University of Minnesota
169,130 kWh during its first season of operation.
The McNamara Alumni Center at the University of Minnesota is designed as a campus showplace. With its granite-covered geodesic-shaped exterior and impressive 85-ft atrium, the 231,000-sq-ft structure is a combined visitor and conference center as well as office building for University staff.
The building is owned by the University Gateway Corporation, a non-profit corporation comprising representatives from the University of Minnesota Alumni Association, the University of Minnesota Foundation, and the Minnesota Medical Foundation. Because of its many functions, the McNamara Center is open during day and evening hours and on weekends. Despite its ultra-modern architecture, the building relied on a single 550-ton chiller for cooling during its first six years of operation. That’s because the mechanical room was built for the single chiller only - leaving little room for chiller failures. An ultra-modern HVAC system had to wait until chiller technology was developed to the point where smaller machines with adequate capacity would fit in the room.
When frictionless chiller technology - with its small footprint - was introduced, Jon McCombs, Alumni Center operations manager for NorthMarq Corporate Solutions, the property management firm, recognized the opportunity to add redundancy to the HVAC system. However, early models were too small for the load requirements, and there wasn’t enough room to add multiple units. “When McQuay introduced the 300-ton frictionless chiller, it gave us both the size and small footprint we needed to redesign the HVAC system,” said McCombs. “In addition to redundancy, our goal was to reduce energy and provide significant life cycle cost savings to the building’s original chiller plant.”
The end result is that the 300-ton McQuay chiller runs about two-thirds of the time, with the 550-ton chiller providing redundancy and carrying larger loads. The new HVAC system reduced energy costs by 10 percent during the first year both chillers were in operation.
Meeting requirements for redundancy
When magnetic-bearing compressor technology did arrive, McCombs saw it as the solution to issues not only of redundancy, but also of energy savings and mechanical room restrictions. McCombs worked with Lindell Engineering (Minneapolis) and completed first designs around a 210-ton stainless steel plate heat exchange chiller. This design saved energy but presented maintenance limitations. Cleaning the condenser required completely taking it apart, and the stainless steel plate added to the unit’s weight.The mechanical contractor on the project, Albers Mechanical, knew of McCombs’ concerns and suggested he consider McQuay’s frictionless chiller, which had just been introduced to the market. “This new chiller technology appeared to give us the compact footprint and part load performance - with the added benefit of extremely quiet operation - that we needed,” said McCombs. Another benefit of the new frictionless centrifugal chiller is that the shell and tube design is easier to service than the steel plate heat exchanger. The equipment supplier, Schwab Volhaber Lubratt (St. Paul, MN), helped spec the new chiller.
Redesigning to save energy
McCombs’ first goal was to improve energy efficiencies in the spring and fall. Because about half of the McNamara Center remains open in the evenings and on weekends for special events, McCombs thought the best energy savings would come from shifting after-hours and spring/fall responsibility to the new McQuay frictionless chiller. That would leave the 550-ton chiller for those hours when it was really needed.During the design phase, McCombs and his team also installed VFDs on both the evaporator (chilled water) pump and condenser water pump (cooling water tower) piping systems and added digital flow meters to monitor both piping systems’ gpm. As a result, they were able to regulate flow and regain some flow loss due to triple-duty valves installed in the original design. Removing the triple-duty valve from the equation increased flows to both the chilled water and condenser loops and further reduced energy lost to the triple-duty valve.
Automatic transfer switch simplifies power-sharing
To take advantage of the existing electrical supply, McCombs installed an equipment automatic transfer switch. The switch transfers power between chillers, depending on which one is running (they don’t operate at the same time). New VFDs adjust flow rates as required for each chiller’s design, which is a big help in simplifying the operation and saving energy. He also installed an amp meter to monitor both chillers’ electrical use from the same source. By selecting the chiller that matches the load, McCombs reduces energy and increases the life cycle of the original chiller. In addition, the new system gives him redundancy to around 85° outdoor air temperature.Another benefit is the ability to integrate with the new Johnson Controls Metasys® energy management system. The chiller communicates control and monitoring information to the Metasys system using BACnet®.
Putting it all together
During its first season of operation, the McQuay chiller faced a higher number of degree days for cooling, compared to the average of the past three years. Factor in the new VFDs and lower gpm in the AHUs, and the new system has saved about 169,139 kWh. At the current local electricity rate (about 7 cents/kWh), that’s 10% less in energy costs compared to operating one non-redundant chiller system. The McQuay chiller is in use about 65% of the time - whenever the part load performance gives the most energy benefit. That can be as low as 0.33 kW/ton IPLV.Seasonal runtime hours on the original 550-ton chiller have been reduced by approximately 1,800 hours. Total chiller runtime hours are approximately 3,000 hrs/yr.
The larger chiller operates for just over one-third of the season. “We’ve learned that, as the frictionless chiller gets close to full load, we achieve additional cost savings by running the larger machine at partial load,” said McCombs.
Working in tandem, the two chillers give the McNamara Center the redundancy and reliability it needs. As a result, McCombs can ensure University staff and guests that they can rely on the building’s cooling effects even on the hottest days, while he’s ensured of saving valuable kWh.ES