
This function space in the King's Grant Inn was replaced with meeting rooms and office space for the new CST facility.
When I was growing up north of Boston in the 1960s, there were many people on the New England north shore who had stories to tell about the King's Grant Inn in Danvers, MA.
Located on what was then coined America's "Technology Highway" (Route 128) this English Tudor wood frame exterior began as a two-story motel. Within the 1960s and '70s it expanded to include a swimming pool, which was later enclosed and was adjacent to function rooms, more guest rooms, and office space. A vibrant place to have your wedding, high school prom, and other functions, time took its toll on this 20thcentury icon. Who would have figured it was ideal for a LEED® biomedical facility, rejuvenated for the 21stcentury?
The lessons learned from this project were grounded in two key success drivers: first, Cell Signaling Technology (CST, the purchaser) and, secondly, Doug Trees, an architect with D.F. Trees Associates (DTA) of Hamilton, MA. Both played significant roles in the rejuvenation of the King's Grant site.
CST, a 10-year-old biomedical firm, was attracted to the facility for several reasons. The land was prime real estate, situated conveniently off Route 128 not far from several major roadways connecting CST to many of the institutions they serve, as well as accessible to railway and air transportation.
The facility is also situated close to the New England shoreline and not that far from the borders of New Hampshire and Maine, which is ideal for employees who want to travel to the city, do some off-road mountain biking, sailing, or simply walk through tranquil historical countryside.
In procuring the land and the buildings on the site, CST had the vision to look beyond what it was, to what it could be. CST produces antibodies used for research on cancer, Alzheimer's disease, diabetes, and other diseases and, in keeping with their reputation as a leader in the health care industry, they also saw innovative opportunities to make the King's Grant Inn something more than a motel stuck in the 20thcentury. CST, a spin off from New England Biolabs (NEB) of Ipswich, MA, drew upon the experience it shared with NEB when it built its "commitment to business and environment" facility in the mid-1990s. Preservation of the environment shared a common bond with preservation of life, which are the products of CST.
Trees, CST's architect, shared this vision and had the experience to see this facility as the optimum example of what LEED Material & Resource credit 1.1 (M&R 1.1) Building Reuse represented to the environment. The lessons learned, many of which are noted herein, are built on credit 1.1 Building Reuse. All the other credits that made this project a certified LEED success revolve around bringing the King's Grant up to 21stcentury energy and environmental standards.
So what can be learned from this experience? How did a totally unpretentious motel and function facility become a biomedical facility success story?
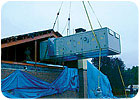
A new AHU was installed to serve the research areas in the new CST facility.
FILM AT 11
The project began in 2004 with the negotiations to purchase the property. This decision coincided with CST's knowledge that they would be in need of more space by 2008, and so, the participants got together to discuss the lessons learned from past projects.A roundtable session seemed like the appropriate forum to discuss the transformation of this complex, the business plan, and how it could be achieved with a commitment to energy and the environment. The owner, the design team, the construction management firm, and the commissioning engineers agreed that this roundtable format should also be captured on film/DVD, which proved to be a very useful business tool to assist in the next stage of CST's growth.
The film would provide the opportunity to quickly draw upon past experience when a refresher course was needed to assess a particular project activity. Pertinent information relative to the building program, redesign of the facility, HVAC design, and building system commissioning from this open session was captured. For others involved with LEED projects, looking back at past jobs as well as closing out a current LEED project, roundtable forums like this team's session will be time and money well invested.
The participants at this meeting included:
The session was informative as each participant brought his experience to the project. For the CST group, it was their first building program, while the rest had several years of building design and construction experience but were looking to learn more. As a result, these conversations provided a wealth of new information to CST about a field of business that they were not regular participants in, as well as knowledge of what they need to do next time.

The King's Grant Inn swimming pool area was retrofitted to accommodate the new interior garden, waterfall, and pool.
ISSUES AND LESSONS LEARNED
Assessment. The design team began their role on the job when they first visited the site and provided an initial assessment of the structure as it pertained to building adaptation to office, research, and lab space. DTA/D&L walked the site, reviewed existing conditions and record drawings, and inspected the existing mechanical and electrical systems. The design and construction budget, in the beginning, was set at $10 million for the 107,000-sq-ft complex.The obstacles to overcome began with the 8-ft, 9-in. floor-to-floor height, the $97/sq ft construction budget, and the antiquated mechanical and electrical systems that had originally been designed for a motel, function space, indoor swimming pool, and office space. The project was shaping up to be a daunting challenge for the design team, and would eventually finish up at $19 million and $170/sq ft, still a truly remarkable construction cost when compared with most biomedical facilities being built at $300/sq ft.
M&R 1.1 was the mantra for project success, and this job proved that reprocessing a structurally sound building can achieve building program goals for far less money than building a new building.
Vision. After walking the site, DTA could envision the guest room area as a lab space, but still the whole complex posed a building program challenge. How could this 1960s roadside motel possess the potential to house a 21stcentury biomedical business? Historically, in New England in the past 20 to 25 years, abandoned warehouses with their 14-ft floor-to-floor heights, expansive floor space, and large windows allowing natural light into these three-story structures have been the building of choice when it came to facility reuse. Only CST and DTA saw M&R 1.1 as a viable solution for the King's Grant complex.
It takes a team's technical experience, blended with creativity, to maximize M&R 1.1 opportunities, and CST and DTA were up for the challenge.
LEED. To add to the challenge, CST was committed to making sure the building was LEED certified. Every square foot of space was valuable, but LEED drove the project to reuse existing building space instead of starting new. To assist in ensuring the building program success and LEED certification, CCC worked closely with the design team to provide pre-construction and construction management services. CCC was as assertive as CST and DTA as the job progressed, but in the beginning responded to design concepts with construction budgets and constructability concerns. CCC's LEED facilitator challenged the team with additional credit considerations in the "Innovation & Design Process" category, as well as registering the project online with the USGBC LEED process.
Lessons Learned. Have the LEED facilitator begin collecting data that supports the credits and do it online, beginning in the design phase. At the same time, this individual should be proactive with "What if ...?" and "What about ...?" types of questions.
Leadership and coordination. It is easier to design a facility from the ground up, but leadership is needed when designing an energy-conscious and environmentally correct used building. Such a project can be the financially correct decision in first cost and sustainable cost. Conversion of motel guest rooms to useful lab space vs. tearing the two-story motel section down and starting anew proved to be an easy decision because the rectangular space worked.
Keep an open mind when assessing an existing building structure opportunity. With the commitment to M&R 1.1, close coordination between the building structure and the HVAC system distribution was critical to the success of this reuse process.
Ductwork. When faced with seemingly unrealistic floor-to-floor height (8 ft, 9 in.), the design team opted for horizontal duct and pipe distribution above the roof enclosed in a new insulated and watertight enclosure. Based on this arrangement, the HVAC engineers would use more vertical distribution than ordinarily used in conventional HVAC design to maximize the reuse of space.
Don't overlook vertical duct distribution as a viable duct design option, similar to how vertical pipe distribution is frequently the solution in reduced floor-to-floor height in new construction.
Team awareness. For CST, sitting in on design discussions raised their awareness of the cost impact based on location of their business groups. As a result, the client worked closely with the team to accommodate HVAC system selections that would reduce the amount of outside air required. By consolidating the chemical lab areas, where 100% air in and out is the traditional approach, this would allow the other 75% of lab and office space to be served by an HVAC system with minimum outdoor air and airside economizer.
Building owners need to work closely with the design team and not take a backseat to the design layout. They need to know the impact space allocation can have on HVAC design from an environmental point-of-view.
In addition to building owners taking leadership in ensuring the project will be more energy and environmentally friendly, endusers need to adjust to the green design culture change. The educated researchers at CST were willing to accommodate change to contribute to more energy efficient, and cost-effective HVAC systems serving their workspace. Safety is a perception as well as a concern, and change in how research was done would change the energy consumption budget via energy conservation. Space management also assisted in reducing HVAC construction cost.
Special expertise. After the initial design team walk-through of the King's Grant site, there was a perception that much of the existing mechanical and electrical systems could be reused. The design engineers were against this approach but the conceptual phase budget put the pressure on the designers to reuse key components of the HVAC, electrical, and plumbing systems, including the boiler. As the job moved through construction, the construction team recognized that some of this equipment and distribution had to be replaced. As the job progressed, the client was also willing to invest more into the infrastructure.
Listen to the design engineer. In the end, much of the infrastructure had to be replaced. If the client was not as involved in this job, change-orders in the construction phase could have come back to haunt the design firm. All too often, HVAC construction budgets are cut and in the end, the HVAC design firm is questioned on why this happened.
Commissioning timeline. While commissioning requirements were injected into the design phase, the third-party commissioning firm was not contracted until the process had moved into the construction phase. The initial perception was that commissioning would be done, but the value of this service was not fully appreciated. The commissioning plan and specification requirements were sprinkled through the contract specification.
Get the commissioning firm fully involved in the schematic phase of the job and establish commissioning compliance in its own division 17000 section of the contract specification.
Commissioning scope. With the LEED process, there was a perception that commissioning would resolve all mechanical and electrical problems. There was clearly a misunderstanding about the role of the commissioning engineer and their scope of work when systems continued to malfunction. RDK noted that the commissioning contract had very clear tasks, systems to be commissioned, and number of construction phase commissioning meetings. This scope was not shared with many of the other team members, so misunderstandings resulted based on expectations. This is a common problem on many commissioned projects. Commissioning services are not provided with a blank check.
The commissioning scope should be shared with all participants and done so at the beginning with a presentation to the project team.
Another perception of the commissioning process is that the commissioning engineer will continue to participate in re-testing when certain parts of a system FPT demonstration failed. RDK noted that re-testing is usually an additional service and that it is important to specify in the contract document phase a commissioning plan that makes sure the systems are truly ready for demonstration to the commissioning team. Specifying FPT criteria should include a test-run by the contractor or construction manager before organizing the commissioning team to observe the demonstration. It was also noted that many of the equipment and system performance troubles were perceived as commissioning issues when they were really design issues, punchlist issues, and/or limitations on the controls that were provided.
A comprehensive commissioning specification, as part of the contract documents addressing the steps leading up to the FPT and the documents, is needed to ensure system readiness.