I’ve heard more than a few stories about catastrophic system failures — most of which were easily avoidable, given their forensic trail to negligent lack of maintenance.
One that comes to mind is a catastrophic fan failure at a Midwestern manufacturing plant several years ago. Naturally, this occurred on a Friday afternoon, grinding the weekend process to a halt and incurring labor to be billed out at weekend rates.
A facility engineer noticed that water temperatures in the 1,200-ton tower were not decreasing sufficiently — yet there were no alarms. A maintenance tech was sent to investigate the tower and found that the fan assembly had blown apart. The fan screens, cylinder, mechanical supports, and other smaller components were damaged as well.
Closer inspection revealed that the fan shaft had significant play due to worn-out bearings, causing the fan blades to repeatedly hit the cylinder. Lacking vibration controls, the entire assembly eventually blew apart, destroying most of the fan section in the process.
Had the tower been subject to routine inspection and maintenance, this very expensive problem — with significant downtime consequences — could have been avoided. Not counting lost production, the owner spent over $20,000 in parts and service alone due to inadequate maintenance and monitoring of fan bearings.
Evaporative cooling equipment, like any mechanical unit of machinery, requires preventive maintenance to maximize its utility.
Simple maintenance procedures provide enormous benefits to a wide range of connected systems and equipment, manufacturing processes, and occupants too. Benefits include the reduction of operating costs, down-time, and capital expenses, and improved system efficiency; even equipment lifespan.
Central to each of these benefits is the prevention of critical or catastrophic failures. Often, repair costs pale in comparison to costs that stem from the downtime loss of production.
Most failures of evaporative cooling equipment involve moving components and can typically be separated into three specific parts or systems:
• the fan motor,
• the fan, and
• drives, or power transmission – bearings, sheaves, and belts.
Evaporative cooling manufacturers provide resources to assist facility personnel with maintaining these components, such as the equipment operations and maintenance (O&M) instructions, and maintenance schedules. These tools often focus on the basic level of maintenance required for proper operation.
There are, however, a range of innovative processes and products designed to provide a greater level of security for the owner or facility manager.
Heart of the System
The fan motor is the heart of the evaporative cooling equipment. Like the human heart, it requires extra care for the well-being of the equipment.
Control sequencing is an appropriate starting point.
“When applied to across-the-line starts as opposed to the application of variable-frequency drive (VFD), it’s critical to limit start-stop sequences to no more than six per hour,” said Scott P. Buckley, senior manager of North America parts for Evapco Inc.
Buckley said each motor start is associated with a spike in voltage, referred to as in-rush current, that increases the motor operating temperature and can lead to motor winding insulation failure. Limiting the occurrence of these protects the motor.
Increasing the temperature control deadband and/or lowering the setpoint are two ways to reduce fan cycling frequency.
VFDs are the preferred method for control of fan motors. However, there are still some concerns, chief among which is the issue of stray currents.
“VFDs simulate a sine wave via on-off switching of current,” Buckley said. “By-products of this are stray currents that often ground themselves at the motor bearings. Failure to address this will result in premature motor failure. “
A simple and cost-effective solution is available in the form of shaft grounding rings. They operate much like a lightning rod and provide a ground for the stray currents outside of the motor housing.
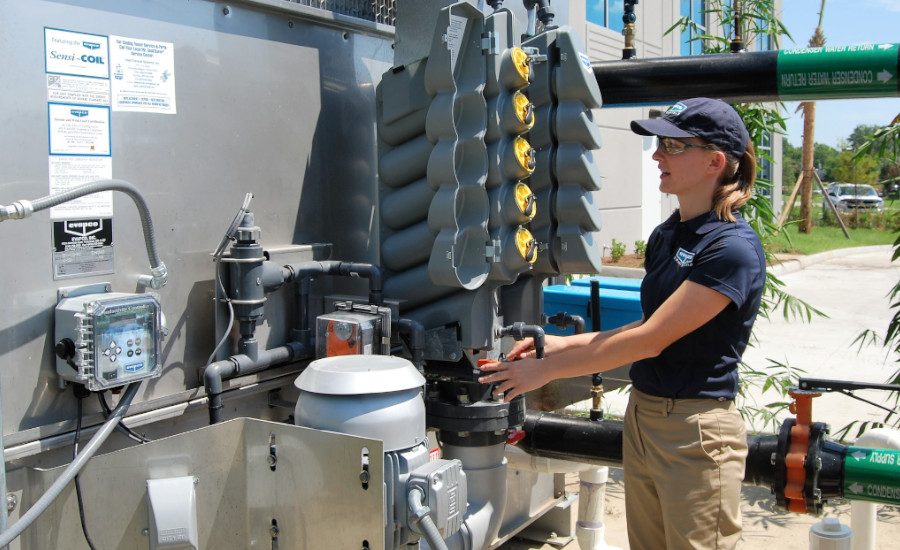
A technician makes an inspection at a cooling tower. Water treatment of cooling towers and condenser water system is a critical component to ensure a long life and proper system operation.
Moisture and Motors
Moisture intrusion is a common mode of failure and can be a very serious challenge.
Yet, evaporative cooling equipment must operate, by necessity, in a humid environment. That’s why fan motors are designed to function properly with some influence by moisture. Consequently, they’re susceptible to moisture contamination, often from condensation.
A key remedy is to ensure that condensate drains are positioned at the lowest point of the motor mounting or enclosure.
The term “totally enclosed” for motors often leads to a false sense of security. The type of motor used for these systems is designed to prevent required cooling air from flowing over the motor windings, but is not airtight.
Another approach, Buckley said, is proactive, greatly limiting the possibility of moisture contamination: installation of space heaters within the motor housing. Space heaters are wired to the motor control panel so that they are energized when the motor shuts off, and de-energized when the motor turns on. This helps to maintain a consistent internal temperature, preventing condensation.
Fan - More Than Meets The Eye
While fans are much less complex than a motor, their maintenance is no less critical. Fan failures are chiefly associated with vibration, balance, or structural impairments. As a result, routine inspection and monitoring are required.
Vibration cut-out switches — designed to protect the fan in the event of excessive vibration — have been a fairly reliable “insurance policy” against fan failures. However, more aggressive approaches will improve equipment dependability.
After all, by the time a fan is vibrating excessively, damage is already occurring, or has occurred, to components such as fan bearings.
A better, smarter approach to assuring fan health comes with the installation of vibration sensors that generate control signals proportional to vibration levels. These devices allow constant monitoring of the drive system and can pinpoint degradation of components long before a failure occurs.
Another key facet of fan maintenance is balancing of the fan. Proper balance is critical to unit operation and performance. Fan balancing can be either static or dynamic. Static balancing is performed when the fan is at rest. Fan suppliers routinely balance fans, statically, following manufacture.
Dynamic balancing, however, is performed while the fan is in motion. Dynamic balance values often differ from static balance values because the fan is subjected to the influence of moving components such as the sheaves and belts.
Any time the drive system is disrupted, the fan system should be dynamically balanced. Disruptions take the form of component replacements — such as a fan, sheave, shaft, or a set of bearings. This will ensure proper operation and increased reliability and longevity.
“Fan blades and fan surfaces should be routinely inspected,” Buckley said. “Corrosion, cracks, gouges and sometimes ice formation, may contribute to fan imbalance, leading to premature or catastrophic fan failure.”
Any corroded surfaces should be sanded and treated with an industrial grade rust inhibitor. Cracks and gouges often result from blade contact with foreign objects. The objects do not require a great deal of size or density given that fans often rotate upwards of 400 rpm or more. Problems like these should be reported to a service company and followed up with a complete unit inspection.
Drive Components
In between the fan motor and the fan are the drive components. Whether gear-driven or belt-driven, proper alignment is critical. Gear drives require coupling between the motor and gear. These can be close couplings or a floating shaft.
Not only can misalignment contribute to a premature failure, but the couplings themselves are under heavy and frequent torque conditions. Because of this, the hardware and flex elements are designed to absorb torque and will usually be the first to show signs of wear.
Regular inspection and timely replacement of these components involve considerably less cost and downtime than a full gear drive or fan failure.
Alignment of belt-driven systems is just as important, although part replacement of belt-driven systems is often less costly and require less downtime than gear-driven systems.
Sheave alignment should result in a four-point contact of a straight edge or laser tool, with a maximum deviation of 1/16-inch. The maximum mid-point deflection of the belt should be 1/2 inch.
Buckley and I know that fan shaft bearings are often the most frequently replaced part of evaporative cooling equipment. Replacements can be reduced with increased care and attention to lubrication.
For starters, use only greases approved by equipment manufacturers. All grease formulations contain some form of detergent, and it’s these chemicals that don’t play well together when mixed. Consistency plays an important role. If new grease is introduced, it’s critical that the entire system C including bearings and lube lines — be fully purged of the old lubricant.
Lubrication schedules are typically provided by equipment manufacturers; these are based on long-term service data — not to be ignored.
Just as important to the schedule is the manner by which bearings are re-greased. Grease is often applied too vigorously — causing bearing seals to blow out — sure to cause premature failure.
Automatic-bearing greasers can be a real advantage. Many are designed to provide a timed release of lubrication. The discharge is performed under low pressure to prevent damage to bearing seals. Despite these advantages, automatic-bearing greasers should not be considered a substitute for visual inspections.
Systematic and thorough attention to the fan and motor assemblies is essential to avoid unexpected interruption of service.