Hot water is an essential requirement for educational environments. From washing hands to daily cleaning tasks, access to a reliable source of hot water is vital. Depending on the school or educational institution's needs, different types of water heaters can be used, such as tankless, traditional storage tank heaters, or heat pumps.
Heat pump water heaters operate differently from traditional water heaters as they work by transferring heat from the surrounding air to heat the water. In recent years, they have become increasingly popular in schools and educational institutions for their efficiency and cost savings.
Harris piping trades superintendent Hector Garcia sat down with regional preconstruction director Andrew Tranovich to discuss his experience on the largest heat pump water heating system installed in an educational institution at the time in the San Francisco Bay Area, and then how a second educational project nearby is going currently. His experiences on these and other projects continue to refine our preconstruction approaches and system risk management.
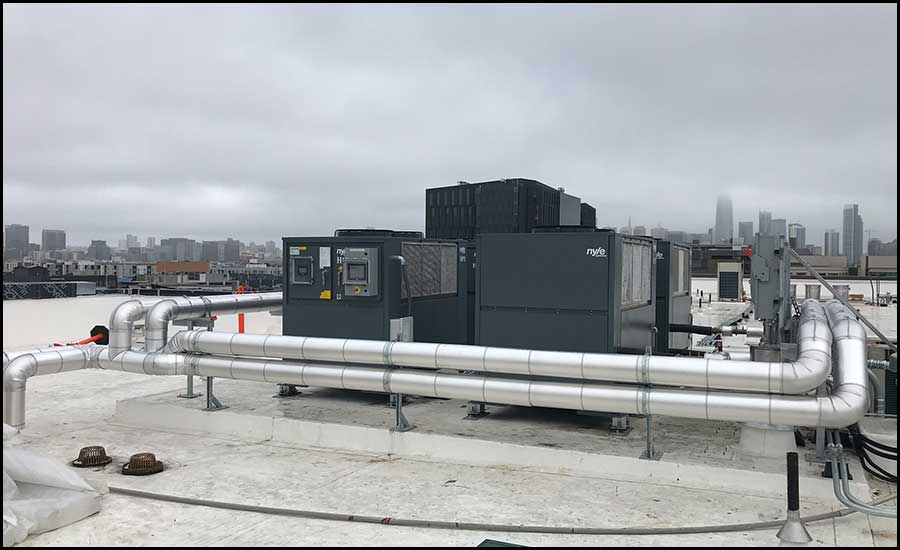
In 2017, a major public academic institution in San Francisco completed a pilot project for heat pump water heaters. The heating plant serves 600 units of student housing in two new-construction buildings, 300 units each. The system was “more like a refrigerant tech system” versus conventional approaches common at the time, which added complexity with tuning and startup and more variables to manage during installation. At the time, the manufacturers were limited on models meeting NSF61 for drinking water standards for potable water use.
The project system layout was driven by necessity and a cautious approach to diversity, placing nine water heaters on the roof with extensive recirculation piping down six floors to eight total tanks at 1,200 gallons of storage each, 9,600 gallons total. Due to spatial constraints from the size of the plant specified, the water heaters and large tanks could not be colocated. Pumps were required to meet minimum of 250 gallons per minute (gpm) circulation to maximize use of water heaters, with 30 gpm minimum flow required.
First Project Basis of Design
As seen in the above 3-D BIM model figure, the significant head pressure requirements on the pumping system are shown in the system layout. Functioning as an open-loop system, the energy to overcome this water column at 30-250 gpm was a consistent energy use requirement from the owner. As the first major installation of this size, the owner also opted for electric resistance pre-heaters added as a safety factor. These required additional electrical circuits and increased first cost.
One might ask, why take the risks with a system like this in the relatively unlimited 2017 equipment procurement environment? Why be the first? Why risk your student housing system performance? It starts with the owner.
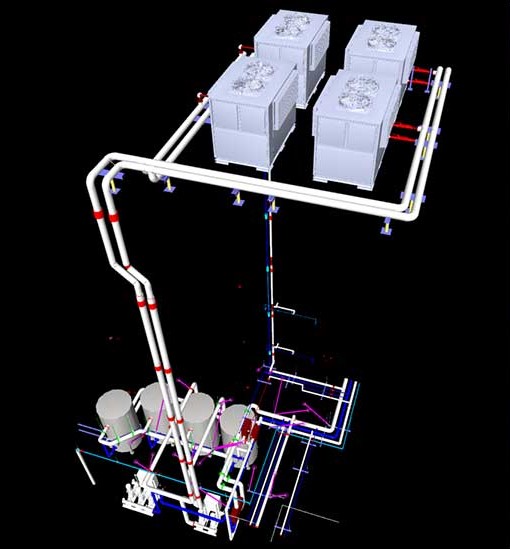
Their basis of design baseline at the time was domestic hot water from air-source heat pumps with no supplemental heating. This underwent multiple discussions and challenges from project staff. What eventually enabled the system proceeding to installation is a combination of vision and support from the owner, with a focus on CO2 emission reduction. The natural gas water heating system compared at the time resulted in 1,509,000 pounds of modeled CO2 emissions annually. The heat pump system installed, including with supplemental electric resistance, resulted in 873,000 lbs of modeled CO2 emissions annually, a drop in carbon emissions of over 42%. In addition, during the layout of the units on the roof, the team planned for future solar and optimized location to permit the maximum number of panels and incident radiation absorption around the water heating equipment.
Differences in the Second Project
Garcia is now overseeing a second and different major academic heat pump water heater project, under construction at the time of publication. While academic use is considerably less demanding than a student housing building, this project size still required heaters, tanks, and circulation piping. This project is different in that it uses the storage tank as a buffer tank duty and not cautiously sized for performance assurance like the prior project.
In the context of 2023, the industry confidence in these systems and their performance has consistently grown, and, as such, is not oversized for service like the first project was. Smaller pumps are in use — smaller 1,000-gallon tanks for a total 2,000 gallons of storage. Because of the relatively downsized tanks, they are able to be placed on the roof and seismically braced adjacent to the water heaters themselves, eliminating the need for an extensive primary side circulation loop that results in significant heat loss and pump energy.
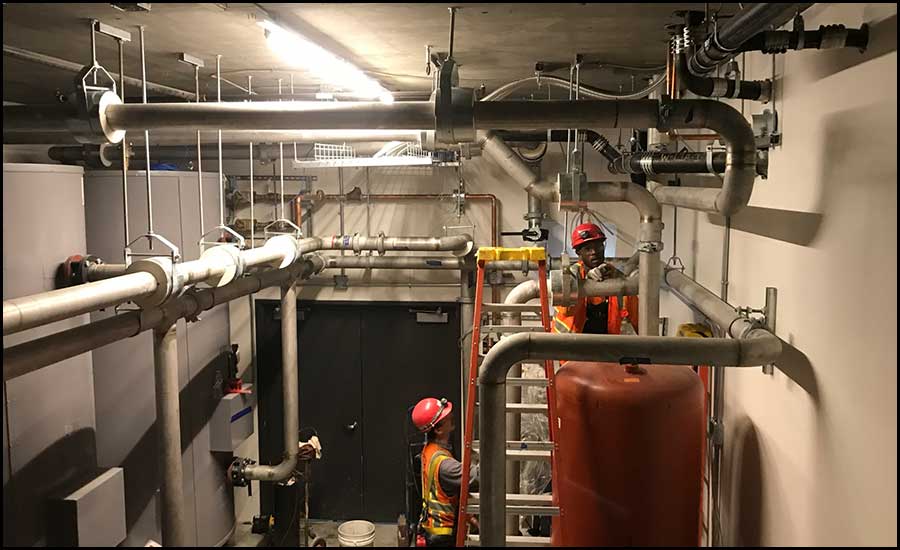
The first project from 2017 consisted of a split plant, with the heating plant on the roof and the large storage tanks in the basement. This configuration was in part required by the conservative approach to the at-the-time unproven project system design driving larger sizes and requiring significant back of house space, served only by the combination of roof and basement. This split plant resulted in additional energy use, including larger primary side circulation pump energy, greater length and size risers and return piping, and consistent heat loss to adjacent spaces from the primary loop and significant tank storage. While the system was fully insulated, the magnitude of heat is still a factor and the basement mechanical rooms maintained an ambient temperature of around 115F.
The Noise Factor
One factor not fully considered during design is heat pump water heating noise. These systems are louder than conventional gas or electric resistance boiler systems. Most of this is due to the larger compressors required for the refrigerant circuit and any associated fans. Architects, engineers and design-build contractors such as Harris, should take into account the noise when selecting the location of the equipment and space adjacencies, the equipment selection criteria, and the vibration isolation applicable to the project. The first project required reworking the vibration isolation by adding different springs and isolation pads after the fact. This could have been prevented by early consultation with an acoustician to provide the best risk avoidance and cost assurance.
Today, heat pump water heating on a central plant scale is a proven approach and engineers can reduce the amount of conservative sizing from systems even five years ago. As the systems are properly tuned and started up, installation teams get more and more familiar with their behavior and become more efficient with cost and schedule. We are starting to see creative use of the produced cool dry air, like adjacent installations for discharging into cannabis drying houses.
It was recently published by the Air-Conditioning, Heating, and Refrigeration Institute that Americans purchased more heat pumps than gas furnaces for the first time in 2022, with 5.9 million heat pumps sold in 2022, compared to 5.4 million gas furnaces. While not used for water heating, this dramatic statistic demonstrates the significant foothold that heat pump equipment has taken in the market. The ever-increasing amount of heat pump technology installed in the built environment has positive benefits to adopters, including lower first costs, more manufacturer models and variety, and a great number of experienced contractors and technicians to support this type of equipment.
Heat pumps are a great option for any educational institution looking to reduce their carbon footprint while also maintaining a reliable source of hot water. Manufacturers are currently ramping up production lines and offerings as the industry demand and legislation around decarbonization take hold. Smaller tanks, better performance density, and smaller plant footprints mean these are an excellent option for schools and educational institutions that want to reduce their environmental impact while saving money on energy costs.