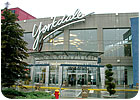
Yorkdale
Shopping Centre’s building management company wanted to reduce the mall’s
energy costs, enhance comfort levels, and simplify management tasks. A BAS was
chosen to integrate the building systems.
Yorkdale was built in 1964, and while the 2-million-sq-ft facility with over 210 stores has pioneered many modern retail-mall concepts, including entertainment complexes and food courts, its existing rooftop units had reached the end of their useful lives. In addition, the original chiller that served the attached 100,000-sq-ft office tower needed updating, a new addition would require its own chilled water system, and a BAS was desperately needed for central control of the entire facility.
The many different projects would require prioritizing and close attention to detail. Fortunately, Yorkdale’s operations manager, John Crane, an engineer by trade, has an eye for details, and nothing makes him happier than implementing changes that will result in serious energy savings.
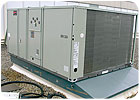
Rooftop
units, with a capacity of 20 tons were chosen for the Yorkdale Shopping Centre
roof. The units have two-stage heating and cooling, which make them adaptable
to Toronto’s weather.
Re-engineering Yorkdale
Crane came to Yorkdale in 2002, after he conducted an operational audit of the shopping center, as well as other properties owned by the building management company. Crane was asked to use the audit to prioritize the upgrades that needed to be performed at Yorkdale.He discovered the first priority was the replacement of the rooftop units, which had reached and/or exceeded their expected life cycle. After that, a BAS needed to be installed, since there was no control over the HVAC or lighting systems, and the office tower chiller needed to be upgraded. In addition, neither the shopping center nor the office tower had received regular upkeep and virtually no capital had been spent on the facilities over the last few years, so a program needed to be implemented to care for the new systems.
“I’ve been practicing energy management since 1979, so it is not new to me,” said Crane. “Three things happen when you embark on an energy upgrade program: You’ll reduce energy costs; you’ll provide a more comfortable environment for tenants, staff, and the general public; and you’ll reduce greenhouse emissions. Performing the energy upgrades resulted in all three of these items happening for us.”
Yorkdale had relied on rooftop units with electric cooling and gas-fired heating to keep the common spaces in the mall comfortable. At the time the shopping center was originally built, the standard practice was to use individually controlled rooftop units, with each unit serving a specific zone in the complex. Individual retailers chose their own equipment, typically rooftop units.
Crane had the advantage of being able to see two to three years of Yorkdale’s energy consumption - that, combined with the operations audit, showed that the rooftops weren’t running efficiently. The rooftops weren’t being controlled or maintained, and they were electrically operated, which resulted in high costs in terms of kWh.
“We did a lot of homework and research, and we decided to install Trane rooftop units,” said Crane. “We liked the way they were designed, the way that the BAS really controlled the components of the unit like the economizers, and the fact that they were a three-speed fan control unit.”
To that end, 11 Trane Voyager™ packaged rooftop units were installed, each with a capacity of 20 tons. These units have two-stage heating and cooling, which makes them adaptable to the wide range of climate conditions in Toronto. In addition, five smaller Voyager Precedent™ units were installed. The Precedent units feature dual compressors, allowing rapid cooldown and longer duty cycles at lower cooling levels. The units are directly ducted to the floors below, with ceiling diffusers for distribution of conditioned air.
Installing the new rooftop units was tricky, since a helicopter was needed to take off the old equipment and replace it with the new equipment. “This required a lot of planning,” said Crane. “We replaced the units, a few at a time, on Sunday mornings before the mall opened at noon.”
All the existing rooftop units were carefully examined before removal to make sure there were no surprises on the day they would be removed. Several curbs needed to be replaced, usually due to age, but for the most part, the new rooftop units fit in the exact same footprints as the old equipment.
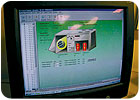
The
BAS allows for total control of the mall’s heating, cooling, lighting, and even
the rooftop units. The BAS also provides an automated PM program that prompts
facilities personnel to clean the filters, check to make sure the economizers
are operating freely, and the belts are not slipping.
Total Control
For a facility as large as the Yorkdale Shopping Centre, it is surprising that no BAS was ever installed to control the heating, cooling, and lighting systems. Crane couldn’t wait to rectify that situation, and he was thrilled when a Trane Summit™ BAS was installed to control the systems, rather than continuing to use local control.According to Crane, the BAS was helpful for a number of reasons. He noted that the central-control capability of the BAS allows precise unit-by-unit scheduling of the rooftop units, thereby reducing energy costs during hours when the shopping center is not in operation. The scheduled operation of the HVAC systems can be easily revised or overridden when necessary, and Crane indicated that the rooftop units are staggered in their ramp-up and ramp-down schedules to control electric demand.
“We have a central control room now, and everything is controlled from that central room - the exterior lights, the interior lights, the rooftop units, the chillers, the whole thing,” said Crane. “We can also look up the systems from the central control room and see how everything’s performing.” The mall and office tower do not have a security system, and the large exhaust fans in the mall that provide smoke control will eventually be controlled by the BAS.
The BAS also provides an automated PM program, so once a month, the program prompts personnel to make sure the filters are clean, economizers are operating freely, the belts are not slipping, and the controls are clean. Crane noted that the use of the new, centrally controlled rooftops, combined with energy savings from the new lighting, has reduced the facility’s annual electric usage from 16 million kWh to 12 million kWh. He believes that about a third of the savings is attributable to the use of more efficient rooftop cooling units, together with their being on a central comfort-control plan. Thus, the new system is saving nearly $120,000/yr.
Installing the BAS was problematic at times, since wires had to be run through the existing shopping center and office tower. As Crane stated, “At times, it was a nightmare. Now that I’m sitting here, I wonder how we did it. There was a lot of re-routing, and when we thought we could go down one chase, we found out that we couldn’t, so we had to re-think everything. From the central control room to some of these rooftop units is a distance of almost a kilometer, but eventually it was finished, and it’s working well.”
Something Old, Something New
While the rooftop units were being replaced and the BAS was being installed, Crane was also upgrading the chiller plant that serves the office tower. The original 200-ton Trane CenTraVac™ centrifugal chiller was installed when the tower was built in 1978. Crane decided to take the opportunity to change it over from R-11 to R-123, which is in compliance with Canadian regulations.The conversion involved disassembling the chiller and replacing all of the necessary elastomeric seals, gaskets, and O-rings. The refrigerant orifice was replaced to optimize performance with the changed refrigerant, and the compressor motor was rewound and replaced. At the same time that the chiller was upgraded, the chiller plant and office tower were also put under the BAS, replacing the original pneumatic control system.
To further improve energy efficiency, VSDs were installed on the cooling tower, chilled water pumps, and the main air handler. In addition, the pumps were refurbished and the chilled water piping was replaced. “The reason I did the upgrades on the chiller and the pumps was just to be more energy efficient,” said Crane. “We probably could’ve gone another 10 years without doing anything, but that’s not how I operate. Operating a building is very expensive, and with me, everything has to do with increased energy efficiency and reduced greenhouse emissions.”
The upgrades have helped increase energy efficiency over the last few years, as well as enhance reliability and tenant comfort until the chiller can be replaced in 2008. The boiler plant for the office tower was upgraded over the last two years, and the original equipment was replaced with three high-efficiency boilers.
While all these renovations were taking place, 160,000-sq-ft of new retail space was being added to the Yorkdale Shopping Centre. The new expansion required approximately 20 new Trane rooftop units, as well as a 500-ton York centrifugal chiller that provides cooling to fancoil units in approximately 24 stores.
The York chiller utilizes R-134a, and Crane found this particular unit to be a little more efficient in terms of kW/ton than some of the competition. A chiller was specified for the new space for the simple fact that there was literally no more room for rooftops. There are approximately 44 rooftop units needed to keep the common spaces comfortable, and individual tenants often have their own rooftop units as well. Crane estimated that there are about 300 rooftop units located on top of the shopping center, resulting in “a sea of rooftop units.”
There were initially some interoperability issues between the Trane BAS and the York chiller, but Trane and York representatives worked together to make the system communicate to Crane’s satisfaction. He noted that while he can’t get every point he’d like to, he’s getting everything he needs to operate the chiller in the most efficient manner. Crane guessed that approximately $500,000 has been spent so far on the HVAC upgrades and renovations. And there is still more to come. Once the 160,000-sq-ft addition was finished, it was discovered that the new part of the shopping center didn’t blend into the existing part of the mall. Renovations costing between $30 and $40 million are currently taking place in order to replace lighting, ceilings, and floors so that the two parts of the mall blend together more seamlessly. Several new rooftop units may be part of this renovation as well.
Crane is looking forward to replacing the upgraded chiller in the office tower with a new chiller next year, and lighting changes, such as the installation of energy efficient lamps, are also being considered. “We’re always looking for things to change that could reduce greenhouse gases. Every time that we change a lightbulb to an energy-efficient light, we’re helping out so that another fossil fuel plant doesn’t have to be built. That’s our goal.”ES