- Checking the design of the vfd installation;
- Checking the contractor’s submittals for the drives;
- Inspecting the installation (static inspection);
- Executing and documenting the vfd start-up;
- Functionally testing the drives;
- Training staff to operate and maintain the drives; and
- Monitoring the operation of the drives.
These activities are performed, coordinated and/or witnessed by the commissioning authority (CA). The CA is usually a professional service provider contracted directly to the owner. In other words, the CA is the owner’s direct representative in charge of project quality.
Checking the Vfd Design
One of the CA’s most important duties is checking the construction drawings and specifications.The location of the vfd is the first element on the CA’s list. The unit should be located in a clean, dry space and mounted on a wall or other vibration-free surface. Mounting the drive on a steel support welded to a pump base is not a good idea because vibration will be transferred to the drive. Mounting the drive below any kind of liquid piping is asking for trouble. Mounting in a dusty environment will impact the cooling ability of the unit and will cause early failure due to overheating.
Many vfd manufacturers require their drives to be derated at altitudes above 3,300 ft (1,000 meters) to account for the decreased cooling obtainable with the “thinner” air. If the project is in a mountainous region at or above this altitude, a request for information (RFI) should be issued to confirm this has been considered.
Finally, the drive must be accessible for maintenance and must have the clear space in front required by the National Electrical Code (can be four ft minimum in some installations). Finally, the equipment room must have adequate lighting.
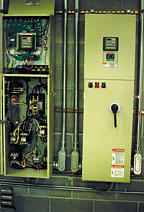
BJT vs. IGBT Drives: What’s the Difference?
A vfd regulates a motor’s speed by changing 60-Hz line-side ac to dc and then back to ac of variable frequency (see Figure 1). It does this by superimposing a series of on and off voltages on a carrier wave. The carrier wave oscillation results in vibrations that cause audible noise at the motor and the drive. This noise has been a major impediment to the wide-scale acceptance of drives in commercial building applications.Over the last five years, manufacturers have gradually made a significant change in the design of many vfd’s. This design change employed insulated gate bipolar transistors (IGBTs) to greatly increase the switching frequency of the drive as compared to the previously used bipolar junction transistors (BJTs). This design change allowed the carrier frequency to be increased from the 1- to 2-kHz range to 10 kHz or higher. The higher frequency quieted the drives (and made motors run somewhat cooler) but also resulted in some undesirable side effects.
As switching frequency increases, the rate of voltage change in the motor lead line increases as well. As this rate of change increases, ever-higher reflected voltages are generated as a result of line reactance. As a practical matter, this means that long line lengths between the drive and the motor are much more destructive in a high-frequency drive than they are in a low-frequency drive. These effects do not appear to be harmful for lower voltage motors such as 120-V or 230-V devices. They are significant for 460-V motors and get worse as the motor voltage increases.
For a 460-V motor, the CA should confirm that the design requires motor lead lengths of no more than 100 ft from the drive. If the lead lengths are any more than 40 ft, inverter duty motors should be specified. They cost more but will last longer and more than justify the higher first cost. The effects of high reflected spike voltages on motor insulation and bearings can be dramatic. They include pitting of bearing races and short circuits at the ends of the motor windings. Motors have been ruined in a matter of months as a result of these effects.
If the vfd carrier frequency can be changed through programming, it should be adjusted as low as possible without causing noise problems. Most noise reduction is usually obtained by increasing frequency from about 2 kHz to 4 kHz. Avoiding frequencies above 6 kHz will reduce motor arcing damage to a minimum. Motors will run slightly cooler at the higher frequencies, but usually there is little benefit above 6 kHz with regard to temperature as well as noise. All this notwithstanding, if the design is checked as described herein, the motor should not overheat or suffer arcing damage at the highest available carrier frequencies of 10 kHz or more.
If a retrofit demands that a vfd be connected to an existing 460-V motor with standard insulation (not inverter duty), the owner should be thoroughly warned that this motor will suffer a shortened service life if the motor lead lengths are more than 40 to 50 ft. For 230-V motors, this effect will be less severe but the motor will still probably suffer some decrease in life. Forewarned is forearmed.
In retrofitting energy conservation projects, vfd’s are frequently installed to improve the control and economy of existing two-speed motors (that were usually part of an earlier energy retrofit). If an existing motor has two-speed windings, the destructive effects of reflected spike voltages due to high switching frequencies is more severe than for a single-speed motor of similar construction. If a two-speed motor is connected to a vfd, the high-speed winding should be used, and the low-speed winding should be left open and taped. If the low-speed winding is shorted, this will cause induced currents in the winding that will cause the motor to run hotter.
Increased running temperature reduces the resistance of winding wire insulation in motors. This reduced resistance allows destructive arcing at lower peak voltages than would otherwise be required. Dusty and humid environments also reduce the voltage required to arc inside the motor.
All of these factors should be weighed when checking the design of vfd applications. After installation these factors should be revisited in light of the actual field conditions.
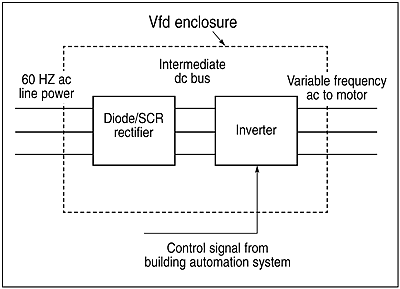
Power Conditioners: Reactors and Filters
A reactor is a device that interacts with the natural frequency of a conductor, vfd, motor, and line transformer to smooth the power waveform and reduce spike voltages. The reduced spike voltages will reduce arcing and extend motor life.A filter is a passive (non-powered) circuit that employs resistance, capacitance, and inductance to allow certain frequencies to pass while blocking others. The energy of the blocked frequencies is dissipated as heat.
Reactors and filters are connected in series in either the “line” (power supply) side of the vfd or the “load” (motor) side (Figure 2). Reactors are simpler and cost less than filters. They are routinely available for vfd’s as factory options and might cost $100 to $300 mounted in the vfd case. Most vfd manufacturers will recommend 1% to 5% impedance on the line side and approximately 3% on the load side if the leads exceed 100 ft. In many cases, the reactance of the building’s primary power step-down transformer is sufficient for the line side and only the load side need be considered further.
Reactors should not be applied indiscriminately. The impedance of the reactor results in lowered voltage at the drive and at the motor that will cause current to increase for a given load. In installations where supply voltage is a problem, reactors should be used only as required to leave the highest possible supply voltage. Reduced supply voltage can result in vfd trips due to low intermediate (bus) voltage or high current. These trips are a nuisance at best and are unacceptable in critical applications.
Filters may be used in special circumstances where long lead lengths, dirty and/or wet motor locations, or other considerations demand. Inverter-duty motors and reactors should always be used before filters are applied.
To summarize, the CA should check the design for short leads from the vfd to the motor and 5% to 3% impedance on the line side of the vfd. If there are exceptions in either area, an RFI should be submitted to the owner and design team.
Verify Those Submittals
After bidding, the CA should be given copies of all equipment submittals for use in verifying equipment quality and preparing the Commissioning Plan. Items of importance include:
- Power conditioning accessories;
- Installation requirements;
- Start-up requirements;
- Manual bypass;
- Control connections; and
- Programming.
In checking the vfd submittals, the CA should confirm that power conditioning accessories are included as specified and as required. The CA should review the manufacturer’s installation requirements and compare these to the actual installation. If there appear to be conflicts, submit the RFI.
The installation and start-up requirements provide the details required for the CA’s installation and start-up checklists. The installation checklist is to be completed by the electrical sub-contractor and verified by the CA. The start-up checklist is to be completed by the CA in the presence of the electrician and the vfd factory representative at the initial operation of the drive.
The CA should confirm the drive has the manual controls required to operate the drive without a control signal and the bypass capability of starting the motor across the line in the event of a failure in the rectifier/chopper circuitry.
Finally, the building automation system (bas) connections should be checked for consistency with the engineer’s sequence of operation and the control schematics, and tentative programming variables should be assigned. The final programming will be done at start-up.
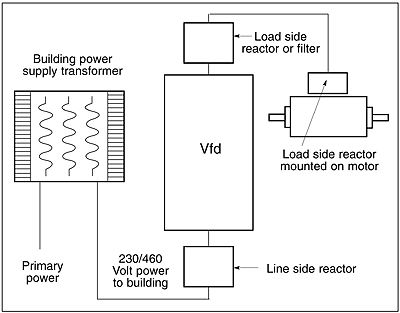
Solidly Installed and Successfully Started
After the drives are installed, the first item on the static inspection agenda is the location. Are drive locations the same as shown on the drawings? Field obstacles can cause major changes in conduit routing, especially on cramped retrofits and remodels. The CA should field-verify lead lengths with the electrician and ask questions if lengths have increased above the 40- to 50-ft thresholds discussed above. Are the drives located in clean, cool, and dry rooms? How about the motors they control?Check the building power supply transformer and confirm its power characteristics, especially impedance. How does this fit with the overall power conditioning needs of the vfd? Are all required connections to the vfd in place including power and control?
Starting the drive for the first time begins with reviewing the programming. In most cases, the drive will have been pre-programmed with a factory default value that will allow the drive to be safely started. But don’t count on it! Each variable must be checked and reviewed in the operation manual to determine its effect on the operation of the attached equipment.
As the drive is first started, it should be ramped slowly up to speed, with someone watching the motor (which may be in a different location) at the same time. The drive should bring the load up to speed and control without excessive hunting, although hunting is best approached after balancing is complete. Operate the unit with the manual controls, and finish by checking for correct status at the bas when operated in the manual mode.
When the drive has been started and programmed, it can be tested under field conditions. This is done by varying the load on the drive and allowing the drive to automatically follow the load. For instance, if the drive controls a fan motor through a duct pressure sensor in a variable air volume (vav) system, all of the vav boxes can be commanded open through the bas. This will drop the pressure in the ductwork and generate a signal through the bas for the drive to increase motor speed.
If all boxes can be activated at once, this test will cause the duct static pressure to change much faster than would occur in normal operation. Even so, the drive should increase motor speed smoothly and should regulate to the required setpoint without excessive hunting. Driving hydronic coil control valves wide open provides a good picture of the response time and stability of the pump vfd. These valves can be driven wide open by changing temperature setpoints in the respective spaces.
Checking Test and Balance
Part of functional performance testing is the verification of the test and balance (TAB) work. Just to clarify the issue, although TAB may be included in the commissioning contract, that is not usually the case. It is more the norm for the TAB to be kept under the general contractor and for the CA to verify the TAB figures. While checking the TAB work, there are at least two issues that should come to mind for the CA regarding vfd’s.The vfd is not to be used as a balance tool for fans. The TAB contractor should adjust the sheaves on the fan and motor so that the fan produces the required maximum air volume at full motor speed. The TAB contractor should not ask the control contractor to program the vfd to limit the motor speed to that required for maximum fan volume. Limiting the motor speed increases the current draw, decreases the motor’s ability to cool the windings, and shortens the life of the motor.
For vav systems, all boxes should be driven wide open and balanced for air volume, and the fan sheaves should be adjusted to this volume at 100% motor speed. The CA should check this for all air-handling units and also confirm current draw, fan speed, and sheave size. This needs to be done with an allowance for dirty filters. When the filters are clean, the fan will run at slightly less than full speed when the balancing is complete. With the filters at the maximum recommended pressure drop, the fan speed will be 100%.
Similar to fans, pump motors should run at full speed with all loads balanced to the maximum. This allows the best motor cooling and longest motor life. If a pump is oversized, trimming the impeller will allow the motor to run at full speed at the required maximum flow. This will provide the best operating economy and the widest range of operation for the pump-motor combination.
O&M Staff Training — The Vital Link
The best time to start O&M staff training on any commissioned project is during static inspection. If the staff has not had any previous involvement during construction, the design engineer should meet with them and the CA and walk through the project. After the walkthrough, the CA should review the Design Intent and the Basis of Design documents, and the engineer should present the system Operation Narrative.These three documents tell the O&M staff (and future staffs) what the building is intended to do, and under what conditions and through what methods it is intended to do it. Then the staff should begin the rounds with the CA for inspection and testing of equipment including vfd’s.
Formal training should be done only after the staff is completely familiar with the intended operation of the building and motor/drive systems. The training should be conducted using the approved O&M manual as the training text and should include the hands-on operation and programming of every drive in the building. Training includes the simulation of drive trips, emergency power situations, and operation of the drive in the bypass mode simulating a drive circuitry failure.
Staying on Top
As training is completed on the drives and the rest of the building equipment and systems, the CA assists in programming the bas to track future building operation. This is done by using the trend-logging feature of the bas to record control variables on key aspects of the building control system. Typically, these include temperatures and pressures for ducts and piping and on-off status for equipment.The trend log is the record that will show the actual operation of the building on a long-term basis. To do that, it needs frequent data points and lots of data storage. Checking space temperatures at 15-min intervals is a good start, but 1-min intervals are recommended to reveal short cycling and hunting for equipment. The 1-min data can be used for fine-tuning vfd’s to get the stable duct and pipe pressures necessary for stable vav box operation, AHU discharge temperatures, and chiller and boiler performance.
While checking the design, the CA needs to confirm that the bas operator workstation has the data storage capacity for this level of datalogging. The storage capacity required will vary with building size and the complexity of the system. But several points of continuous logging should be available for every major piece of equipment including boilers, chillers, vfd’s, and AHUs, as well as some representative space temperatures. Asking questions about this in the design stage will ensure a successful trending operation. Spending some time and energy on the trending, especially during the first-year warranty period, will set the stage for years of economical and efficient operation and a productive workplace. ES