The A/E and construction industries have been working to mitigate global climate change for more than four decades. While we have made gradual progress in every sector, we are still faced with an urgent climate emergency and a pressing need to accelerate our decarbonization efforts before the extreme environmental impacts become irreversible.
Because building construction and operations account for 39% of total global greenhouse gas (GHG) emissions, architects play a vital role in reaching international decarbonization targets and ultimately net zero by 2050. Building operations and energy use account for 28% of these GHG emissions and are referred to as operational carbon. The other 11% come from embodied carbon: The GHG emissions resulting from building material manufacturing, transportation, installation, maintenance, and disposal.
The Problem: Reducing Embodied Carbon
To reduce total carbon in the built environment we must tackle not only operational but also embodied carbon. Carbon emissions generated before a building starts to be used, often referred to as upfront carbon, will grow to an estimated half of the entire carbon footprint of new construction between now and 2050. This carbon impact is immediate and irretrievable once construction is completed. How can we reduce this embodied carbon not just upfront but over the full life cycle of a building?
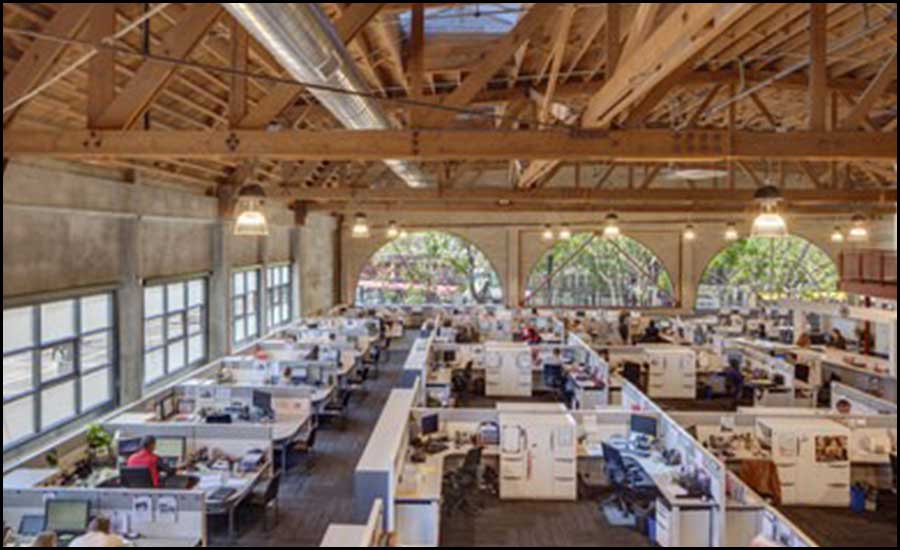
The most effective and immediate solution for embodied carbon reduction in buildings is to use less material and to minimize the use of high carbon-impact materials, such as concrete, metal and glass, which are fundamental for foundations, structures, and building envelopes. Accordingly, the demand for adaptively reusing existing buildings is growing more than ever. The National Trust for Historic Preservation estimates that building reuse results in about 44% less environmental impact compared to new construction.
This shift to more adaptive reuse will put increased focus on the environmental impacts of interiors projects such as expansion, renovation and interior fit out. Conventional thinking has been that compared to the foundation, structural components and envelope, the embodied-carbon contributions from interior elements are a relatively small fraction. However, life cycle assessment (LCA) shows that interiors may have an equal or more significant impact due to the recurrence interval of interior renovations.

The average recurrence interval of tenant improvement (TI) is about 15 years over a building lifetime of 60 years. If we total the carbon impacts of recurring MEP and TI renovations with that interval, the combined renovation impacts can exceed the initial construction impacts, especially in the context of a commercial office building’s lifespan.
The Solution: Designing for the Entire Life Cycle
Efficiency and flexibility are the top interior design priorities for embodied carbon reduction. We must reduce the required physical footprint and extend the life of the building, but at the same time must meet functional needs and promote improved user experience. Interestingly, the best design approaches are not brand new but reflect what we’ve been implementing for the last three decades in terms of open plans, modular systems, free addressing, office sharing, and alternate workspace for an agile workplace. What we need to do now is maximize how these concepts can allow for net-zero reuse of interior spaces over time.
This focus on reuse emphasizes a design approach that allows for easy replacement — such as modular design, self-contained unit layout, or a kit-of-parts concept — as well as design for disassembly, reversible design and an end-of-life plan. As a result of the COVID-19 pandemic, the turnover of interior fit outs for office spaces may become more frequent, making these design principles even more essential for achieving an owner’s environmental and economic goals.
We typically select interior finishes using different criteria for each project: client preference on look and feel, functional performance, durability, cost, chemical-free, biophilia, etc. However, the environmental impacts of materials should be added as a basic threshold. We should set the carbon budget and benchmark baseline for every project at the beginning of the project. By calculating whole-building LCA, especially embodied carbon emissions at each project design phase, we can establish quantitative data for high- and lower-impact materials that will inform more sustainable design decisions.
In addition to optimizing material type and quantity, we also need a paradigm shift in aesthetics. This means we would avoid energy intensive interior finishes used for decorative purposes only. We would expose the building structure and building system itself as much as possible and appreciate the structural integrity and natural materiality, such as the grain of biogenic material and the natural patina of less processed or refurbished finishes. At the same time, manufacturers should implement better transparency along with take-back programs, renewable energy, increased durability, low-carbon-emitting technology, and even carbon capture and storage technologies.
Workplace designers should emphasize the circularity concept in the early stage of office design. Predesign program considerations should include increasing efficiency and flexibility as well as addressing the full life cycle of interior spaces and materials, including end of life. During the design phase, reconfiguration scenarios and disassembly options should be demonstrated by comparing environmental impacts through LCAs. Construction documents should specify the detailing of modular units, disassembly of components, and the recycled content and reuse of materials.
This LCA integrated design workflow will eventually maximize the value of a project by reducing environmental and construction costs, optimizing environmental performance and building footprint, improving occupants’ existential health and productivity, and enhancing the organization’s brand. It’s also increasingly likely to become a permitting requirement. California passed legislation in September 2022 that sets accelerated targets for embodied carbon reduction in new building projects, making LCAs a fundamental part of a compliant design process.
The good news is that we already know how we can achieve net-zero carbon in the built environment, thanks to the collective work of architects and engineers around the globe. This offers a very promising and encouraging opportunity for the A/E industry to take the lead in reaching not only carbon neutrality but that moment when the amount of carbon stored in a building exceeds the amount emitted during materials manufacturing and installation: the carbon positive future.
As demonstrated by two additional case studies of projects that have already achieved significant embodied carbon reductions or even carbon-storing solutions, interior design will play a pivotal role in building our carbon positive future.
Editor’s Note: This article originally appeared on SmithGroup’s Perspective blog. See the original post in its entirety here: https://www.smithgroup.com/perspectives/2023/designing-a-carbon-positive-future-part-1.